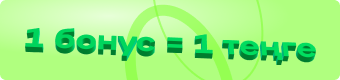
Бонусты жинап картаңызға (kaspi Gold, Halyk bank) шығарып аласыз
Химия пәнінен зертханалық жұмыс
№I ЗЕРТХАНАЛЫҚ ЖҰМЫС
КАУСТІК СОДАНЫ ЭЛЕКТРОХИМИЯЛЫҚ ӘДІСПЕН АЛУ
1. Жұмыс мақсаты:
-
Каустік соданы электрохимиялық әдіспен алу технологиясымен
танысу. Натрий хлориді ерітіндісінің электролизі кезіндегі негізгі электродты процестерді оқып үйрену.
2) Процестің технологиялық көрсеткіштерін анықтау: электролиз
өнімдерінің ток бойынша шығымын және электр энергиясының қолдану дәрежесін есептеу.
-
Электролиз параметрлерінің (процестің ұзақтығының, ерітіндінің
концентрациясының, ток күшінің) процестің негізгі көрсеткіштеріне әсерін анықтау.
2 Теориялық мәліметтер
2.1 Электролиз туралы жалпы мағлұматтар, электрохимиялық процестердің сипаттамасы
Электролиз дегеніміз ерітінділер және электролит балқымалары арқылы электр тогын өткізгенде электродтарда жүретін процесс. Электролиттер дегеніміз ерігенде не балқығанда, ерітіндіге не балқымаға электр тогын өткізу қабілетін беретін заттар. Сонымен қатар электролиттерді екінші текті өткізгіштер деп те атайды. Натрий хлоридінің сулы ерітіндісі қолдануға ыңғайлы электролит болып саналады. Электролиттер еріген кезде оң және теріс зарядталған бөлшектерге – иондарға (аниондар мен катиондар) ыдырайды. Олар электролиттерге ерекше қасиеттер береді.
Электролиттер екі негізгі топқа бөлінеді: күшті (иондарға толық диссоциацияланады) және әлсіз. Күшті электролиттер салыстырып қарағанда аз болады. Оларға сілтілі және сілтілік әсері бар металдардың минералды тұздары, галогенидтер және кейбір ауыспалы металдардың перхлораттары және нитраттары жатады. Минералды қышқылдар мен сілтілер тек барынша сұйытылған сулы ерітінділерде ғана күшті электролит бола алады. Әлсіз электролиттерге органикалық тұздар, қышқылдар және негіздер, сонымен қатар ерітіндіде көп зарядты иондар түзетін көптеген бейорганикалық заттар жатады. Электролиттерде реакция басталуы үшін тұрақты электр тогын беру керек. Электролиттерге электр тогы электродтардың көмегімен беріледі. Оң зарядталған электродтың (анодтың) бетіндегі иондар, молекулалар және атомдар электрондарын береді, яғни анодта электрохимиялық тотығу реакциясы жүреді. Ток көзінің теріс полюсіне қосылған электродта (катодта) электрондардың қосылуы жүреді, яғни катодта электрохимиялық тотықсыздану реакциясы жүреді.
Электролит ерітіндісі не балқымасы арқылы электр тогын өткізу уақытының, электр тогының мөлшерінің және өндірілетін не шығындалатын заттардың мөлшерлерінің арасында Фарадей заңдарымен анықталатын нақты сандық қатынастар бар.
Фарадейдің 1-ші заңы: Электролиз кезінде бөлінетін заттардың мөлшері электролит арқылы өткен электр тогының мөлшеріне тура пропорционал.
Фарадейдің 2-ші заңы: Әр түрлі электролиттер арқылы бірдей электр мөлшерін өткізгенде электродтарда бөлінетін заттардың мөлшерлері олардың электрохимиялық эквиваленттеріне пропорционал болады.
Электр мөлшері кулон (ток күші І ампер болғанда І секундта өткен электр мөлшері), немесе ампер–сағат (І ампер-сағат = 3600 кулон) бірлігімен өлшенеді. Бір грамм–эквивалент затты алуға шығындалатын электр мөлшері тұрақты сан болып табылады, оны Фарадей саны деп атайды. Фарадей саны 96500 кулон = 96500 ампер-сек. = 26,8 ампер–сағ. тең.
1 ампер-сағат электр мөлшері өткенде электродта түзілген заттың мөлшері сол заттың электрохимиялық эквиваленті деп аталады. Заттың атомдық салмағын (А) біле отырып, оның электрохимиялық эквивалентін (Е) есептеуге болады:
|
(1.1) |
Электролиз процесінің нәтижелілігі келесі параметрлермен және көрсеткіштермен сипатталады: ток күші, кернеу, ток тығыздығы, ток бойынша шығым, электр энергиясын қолдану дәрежесі және электр энергиясының шығын коэффициенті.
Электролизерлердегі (электролиз жүретін аппарат) ток күші оның өнімділігін сипаттайды. Электролизер арқылы өтетін ток күші неғұрлым көп болса, электролиз процесінде алынатын өнімнің шығымы соғұрлым жоғары болады.
Электролизердегі нақты кернеу бірнеше құраушылардан тұрады.
Uтәж.=Uт+Uконц+ Uасқ..+J·R |
(1.2) |
мұндағы: Uт – ыдыраудың теориялық кернеуі, в. |
Uт=aт- кт |
(1.3) |
мұндағы: aт және кт – анодты және катодты реакциялардың тең әсерлі потенциалдары, в. |
Uконц – концентрациялық поляризация, в:
Uконц=(a.конц -k.конц ) |
(1.4) |
Uасқ. - анод пен катодтағы асқын кернеу потенциалы, в:
Uасқ..=(a-к.) |
(1.5) |
мұндағы: a және к – анодты және катодты асқын кернеулер, в. J·R – омдық кедергілер қосындысы, яғни электролиттің, диафрагманың, электродтардың, ток өткізгіштерінің омдық кедергілеріне шығындалатын кедергі. |
Натрий хлоридінің қаныққан ерітіндісінің электролизі кезіндегі анодтың және катодтың тең әсерлі потенциалдары:
aт=+1,33в, кт= − 0,84в.
Электролиз кезінде омдық кедергілер қосындысының және поляризацияның шамасын төмендету арқылы электролизердегі кернеуді азайтуға тырысады. Ыдырау кернеуі әрекеттесуші заттың табиғатына байланысты болғандықтан оны өзгерту мүмкін емес.
Ток тығыздығы дегеніміз электролизер арқылы өтетін ток күшінің электрод бетінің шамасына қатынасы (а/м2). Ток тығыздығының шамасы электрод бетінің бірлігінен алынатын өнімнің мөлшерін, яғни электролизердің өнімділігін анықтайды. Сондықтан, егер ток тығыздығын жоғарылатқанда өнімнің шығымы азаятын болса, онда ток тығыздығын мүмкіндігінше жоғарылатуға тырысады.
Ток бойынша шығым () дегеніміз электролиз кезінде алынған заттың мөлшерінің (Gтәж) оның Фарадей заңы бойынша алынуға қажет мөлшеріне (Gt) қатынасы:
= |
(1.6) |
«Ток бойынша шығым» деген түсінік химиялық процестегі өнімнің шығымы деген түсінікке сай. Заттың теориялық мөлшерін Фарадейдің екі заңын біріктіретін теңдеу бойынша есептейді:
Gтеор= |
(1.7) |
мұндағы: А - электролиз барысында алынатын заттың атомдық салмағы, г; J - ток күші, а; - электролиз ұзақтығы, сағ; n – катионның валенттілігі; F- Фарадей саны, а·сағ. |
Электр энергиясын қолдану дәрежесі () дегеніміз энергияның теориялық қажетті мөлшерінің (Wтеор.) оның электролиз кезінде шығындалған тәжірибелік мөлшеріне (Wтәж) қатынасы:
= |
(1.8) |
Энергияның теориялық шығыны (Wтеор.) келесі формула бойынша есептеледі:
Wтеор=UтеорJ/Gтеор |
(1.9) |
Электролиз барысында жұмсалған энергияның тәжірибелік шығыны (Wтәж). келесі формула бойынша есептеледі:
Wтәж= Uтәж.J/Gтәж |
(1.10) |
-
Каустік соданы алудың электрохимиялық әдісі
Натрий хлориді ерітіндісінің электролизі – сулы ерітіндідегі электрохимиялық процестің негізгі мысалы болып саналады. Бұл процестің нәтижесінде құнды өнім каустік содамен (NaОН) қатар сутегі және хлор алынады.
Электролиз процесі тор немесе тесіктері бар табақшалар түрінде жасалған темір катоды бар диафрагмалық немесе сұйық сынапты электролизерлерде жүргізіледі. Анод ретінде графит қолданылады. Өнеркәсіпте торлы болат катодқа тығыз орналасқан сүзгіш диафрагмасы бар электролизер қолданылады. Натрий хлоридінің қаныққан ерітіндісі анод кеңістігі арқылы беріледі. Ол гидростатикалық қысым әсерінен кеуек диафрагма арқылы сүзіліп, катодты жуып өтеді.
Натрий хлориді суда келесі схема бойынша ыдырайды:
NaCl ↔ Na++Cl- |
(1.11) |
H2O ↔ H++OH- |
(1.12) |
NaCl ерітіндісі арқылы тұрақты ток өткенде анодта Cl- және ОН- иондары разрядталады, ал катодта Na+ және H+ иондары. Анодта келесі тотығу-тотықсыздану процестері жүруі мүмкін:
2OH- – 2ē H2O+0.5O2 |
(1.13) |
2Cl--2ēCl2 |
(1.14) |
Ал катодта келесі реакциялар жүруі мүмкін:
Na++ēNa |
(1.15) |
2H++2ēH2 |
(1.16) |
NaCl-ң қаныққан ерітіндісіндегі анодтағы ОН- ионының разрядталуының тең әсерлі потенциалы +0,82в, ал Cl- ионының разрядталу потенциалы +1,33в. Графитті анодтағы оттегінің асқын кернеуі хлордың асқын кернеуінен жоғары болғандықтан, алдымен Cl- ионы Cl2-ні түзіп разрядталады. Ерітіндінің концентрациясының төмендеуімен хлор разрядының потенциалы жоғарылайды. Сондықтан процесте құрамында 310-315г/л NaCl бар қаныққан ерітінді қолданылады.
Темір катодта Na+ ионын разрядтау үшін электродтағы кернеу Н+ ионның кернеуінен 6,5 есе көп болуы керек (Na+ ионы үшін –2,71в, ал Н+ ионы үшін –0,415в). Бірақ электролизерде мұндай кернеудің болуы мүмкін емес, сондықтан тек Н+ ионы ғана разрядталады. Ал Na+ және ОН- иондары катодтық кеңістікте жиналып күйдіргіш натр түзеді:
Na++ OH-↔ NaOH |
(1.17) |
Жалпы электролиз процесі мына теңдеумен өрнектеледі:
2NaCl+2H2O=Cl2+H2+2NaOH |
(1.18) |
Электролиз процесінде электролиттердің құрамындағы иондардың ішінен теория жүзінде ең аз электродты потенциалы бар ион ғана разрядталады.
Электролиз барысында негізгі процестермен қатар жанама процестер де жүруі мүмкін. Жанама реакциялардың әсерін азайту үшін асбесті сүзгіш диафрагма қолданылады. Жанама процестерге газды хлор мен оттегінің ерітіндінің басқа компоненттерімен әрекеттесуі жатады. Хлор жарым-жартылай аналитте еріп, су және сілтімен әрекеттесуі нәтижесінде натрий хлориді, хлораты мен гипохлориті түзіледі:
Cl2+H2O ↔ HCl+HСlO |
(1.19) |
HClO+NaOH ↔ NaClO+H2O |
(1.20) |
HCl+NaOH ↔ NaCl+H2O |
(1.21) |
3NaClO ↔ NaClO3+2NaCl |
(1.22) |
Анодта ОН ионының разрядталуына байланысты (1.14) теңдеуі бойынша өте аз болса да оттегі бөлінеді, ол графитті анодтың көміртегісі мына реакция бойынша әрекеттеседі:
С+O2 = СO2 |
(1.23) |
Жанама процестер негізгі өнім бойынша ток шығымын төмендетеді, әсіресе электр тогының көп бөлігі NaClO-ның NaClO3–ке дейін тотығуына шығындалады. Жанама процестерді болдырмау немесе оларды азайту үшін электролиз өнімдері араласпауы керек. Сол себептен анод және катод кеңістіктерін бөліп тұратын дифрагма қолданылады.
Ток бойынша шығымды жоғарылату мақсатымен жоғары концентрациялы электролит (310-315г/л қаныққан ерітінді) қолданылады. Температураны 70-800С–ге дейін жоғарылату электролизердегі кернеуді төмендетуге және электр энергиясының меншікті шығынын азайтуға мүмкіндік береді.
Каустік соданы электрохимиялық алу әдісінің химиялық әдістермен салыстырғандағы артықшылықтарына: 1) технологиялық процестің қарапайымдылығы; 2) шикізат пен энергияның толық қолданылуы;
3) бірнеше құнды өнімдердің алынуы және 4) өнімнің жоғары сапасы жатады. Электрохимиялық процестердің негізгі кемшілігіне электр энергиясының жоғары шығыны жатады, ал электр энергиясына кететін шығындар өнімнің өзіндік құнының маңызды бөлігін құрайды. Электрохимиялық өндірістерде электр энергиясын тиімді қолдану маңызды мәселе болып саналады.
3 Қондырғының сипаттамасы және жұмысты орындау әдістемесі
3.1 Қондырғылар, техникалық және аспаптық құралдар:
1. Диафрагмалы электролиздік қондырғы
2. Химиялық ыдыстар
3. Титрлеу қондырғысы
4. Liston А 1210 аквадистилляторы
3.2 Қондырғының сипаттамасы
Мерзімді жұмыс істейтін электролизердің зертханалық қондырғысының сызба-нұсқасы 1.1-ші суретте көрсетілген.
Ас тұзының сулы ерітіндісін электролиздеуге арналған қондырғы айнымалы токты түзеткіштен (18), диафрагмалы электролизерден (21), ток күшін реттейтін реостаттан (17), амперметрден (19) және вольтметрден (20) тұрады. Электролизер қораптан (4) және қақпақшадан (16) тұрады. Қорап пен қақпақшаға қысу өзегінің (5) көмегімен электролизердің конусты түбі (10) бекітіледі. Электролизердің ішіне ток өткізгіш сақина (9), торлы темір катод (8), көлденең асбестті диафрагма (7) және резеңке тығыздағыш (6) орналастырылған. Қақпақшаның бетіне NaCl-ң қаныққан ерітіндісін электролизерге беруге арналған үріңке (1), көлденең дискілі (3) көмірлі анод (2) және хлор мен сутегіні шығаратын шыны түтікше (15) орналастырылған. Ток (13) және (14) (катодты және анодты токөткізгіштер) нүктелерге беріледі. Электролизер тіреуіштерге (12) орналастырылған, ал электролизердің түбіне (10) өнімді жинайтын өлшемі бар ыдыс (11) қойылады.
Асбестті қоспаны катодта тұндыру арқылы сүзгіш асбесті диафрагма дайындалады. Бұл үшін 20-30г. асбесті ұнтақтап, су қосып 15-20минут аралығында біркелкі қоспа түзілгенше қайнатады. Алынған қоспаны (Бюхнер үріңкесін және Бунзен колбасын қолданып) вакуум-сорғыштың көмегімен тесік темір катодтың бетіне сүзіп алады. Диафрагманың беріктігін қамтамасыз ету үшін тесік темір катодтың бетіне сүзетін мата орналастырылады. Темір катодты диафрагмамен бірге электролизердің алынатын бөлігіне орналастырып, үстіне цилиндр қорап пен қақпақшаны қойып болттармен бекітеді.
3.3 Жұмысты орындау тәртібі
1. Қондырғының жинау дұрыстығын және өлшеуіш құралдарының дұрыс қосылуын тексереді.
2. Анодтық кеңістікке натрий хлоридінің берілген концентрациялы ерітіндісін графиттік диск толық және анодтың өзегінің жартысы батып тұратындай етіп құяды.
3. Қондырғыны ток көзіне қосып, реостаттың көмегімен берілген ток күшін орнатады. Ток күшінің мәнін тәжірибенің соңына дейін тұрақты етіп ұстайды. Вольтметр мен амперметрдің көрсеткіштерін жазып алады.
4. Тұрақты ережені қамтамасыз ету мақсатымен берілген шарттарда электролизді 20минут аралығында жүргізеді, содан кейін катодты кеңістіктен 2-3сынама алып талдау жүргізеді. Талдау жүргізу үшін сынаманы келесі тәртіппен алады: электролизердің түбіне 25мм-лік өлшеуіш цилиндрді қойып, секундомерді іске қосып, 10минут аралығында катодты сұйықтықты жинайды. Содан кейін екінші сынама алу үшін цилиндрді басқа цилиндрмен алмастырады.
5. Алынған католиттің көлемін өлшеп, конусты колбаға құяды. Цилиндрдің ішін дистилденген сумен жақсылап шайып, жуындыны да колбаға құяды. Егер бастапқы сынаманың көлемі 10мл-ден көп болса, онда талдау жүргізу үшін пипетканың көмегімен оның 5мл-н алады.
6. Конусты колбадағы ерітіндіге индикатор ретінде 2-3тамшы фенолфталеин тамызып, 0,1н НCl ерітіндісімен титрлейді. Егер индикатор ClO- ионының әсерінен түссізденіп кетсе, онда ерітіндіге сутегінің асқын тотығының 30%-қ ерітіндісінің 2-3мл қосып әдеттегідей титрлейді.
7. Титрлеу нәтижелері бойынша католиттегі күйдіргіш натрийдің концентрациясын (г/л) CNaOH есептейді:
CNaOH= |
(1.24) |
мұндағы: V – сынаманы титрлеуге кеткен 0,1н НСІ ерітіндісінің мөлшері, мл; V1 – титрлеуге алынған католиттің көлемі, мл; К – 0,1н НСІ ерітіндісінің түзету коэффициенті; 0,004 – 0,1н НСІ ерітіндісінің 1мл-гі NaOH-ң мөлшері. |
4 Электролиздің технологиялық көрсеткіштерін есептеу
Электролиз процесінде энергияны тиімді қолданудың негізгі көрсеткіштері ретінде ток бойынша шығым және энергияны қолдану дәрежесі қолданылады.
-
Ток бойынша шығымды (1.6) формула бойынша есептейді. Ол үшін
алдымен электролиз кезінде алынған заттың мөлшерін есептейді:
Gтәж= CNaOH V2/1000 |
(1.25) |
мұндағы: V2 - өлшеуіш цилиндрде жиналған католиттің көлемі, мл. |
NaOH-ң теориялық мөлшері (1.7) формула бойынша есептеледі. Содан кейін күйдіргіш натрдың ток бойынша шығымы ((1.6) формула) есептеледі.
2. (1.8) формула бойынша электр энергиясының қолдану дәрежесі есептеледі. Ол үшін алдымен электр энергиясының теориялық (Wт) және тәжірибелік (Wтәж) шығындары сәйкесінше (1.9) және (1.10) формулалары бойынша есептеледі. Бұл кезде ток бойынша шығым арқылы көрсетілетін тәуелділікті алуға болады:
= |
(1.26) |
3. Барлық тәжірибелік мәліметтер мен есептеулер нәтижелері 1.1 және 1.2-ші кестелерге енгізіледі.
1.1 кесте - Электролиз процесінің тәжірибелік мәліметтері
Сынақ № |
Сынақ алу уақыты (τ), мин |
Ток күші (?), а |
Кернеу U, в |
Католиттің титрлеуге алынған көлемі V1, мл |
Католиттің 10 минутта алынған көлемі (V2), мл |
0,1н НСІ-ң титрлеуге кеткен мөлшері (V), мл |
|
Uтеор |
Uтәж |
||||||
|
|
|
|
|
|
1.2 кесте - Электролиз процесінің көрсеткіштері
Бастапқы ерітіндінің концентра-циясы (СNaCl), % |
Сынақ № |
NaOH-ң концентра-циясы (С), г/л |
NaOH-ң мөлшері, г |
Ток бойынша шығым (), % |
Электр энергиясын қолдану дәрежесі (μ), % |
|
Gтеор |
Gтәж |
|||||
|
|
|
|
|
|
|
1.1 сурет - Мерзімді жұмыс істейтін электролизердің қондырғысы. |
Есептеулер нәтижелері бойынша процестің көрсеткіштерінің электролиз уақытына және католиттегі NaOH-ң құрамына тәуелділігін анықтайды. Зерттеулік жұмыстарды жүргізу барысында ас тұзы ерітіндісінің концентрациясының ток бойынша шығым мен электр энергиясын қолдану дәрежесіне әсерін зерттейді және электролиз процесінің тиімді технологиялық ережесі бойынша қорытынды жасайды.
№2 ЗЕРТХАНАЛЫҚ ЖҰМЫС
СОДА ЕРІТІНДІСІН КАУСТИФИКАЦИЯЛАУ
1. Жұмыс мақсаты:
-
Сода ерітіндісін каустификациялау процесімен танысу
-
Процестің параметрлерінің сода ерітіндісін каустификациялау дәрежесіне әсерін тәжірибе жүзінде және виртуалды зерттеу.
-
Зертханалық жұмысты виртуалды ережеде компьютерлік бағдарлама бойынша орындау дағдыларын игеру.
2 Теориялық мәліметтер
2.1 Каустік соданы химиялық әдіспен алу
Сода ерітіндісінің каустификациясы әктік әдіспен күйдіргіш натрий алудың негізгі сатысы болып саналады. Сонымен қатар, каустификация сульфатты әдіспен целлюлоза, ылғал сілтілі әдіспен саз алу және т.б. өндірістердің бір сатысы болып табылады.
Каустификация төменгі температурадағы әртекті катализсіз процестерге жатады. Бұл процесс ізбесті-содалы тәсілмен суды жұмсарту үшін де қолданылады. Пайда болатын тұнбаның бөлшектерінің өлшемдерін үлкейту, яғни қалдықтың тұну жылдамдығын жоғарылату үшін суды алдын-ала тазартудың кешенді реагентті тәсілі қолданылады. Бұл тәсілде сода ерітіндісі мен әкті алдын-ала араластырып, қыздырып содан кейін суға қосады. Бұл жағдайда сода ерітіндісінің каустификациясының нәтижесінде кальций карбонатының тұнбасы түзіледі:
Na2CO3
+
Ca(OH)2
|
(2.1) |
Бұл тәсіл аммиакты әдіспен кальцийлі сода өндірісінде натрий хлорид ерітіндісін кермек тұздардан тазарту үшін де қолданылады.
Күйдіргіш натр өндірісінде шикі бикорбанатты декарбонизациялау немесе кальцийлі соданы еріту арқылы алынған сода ерітіндісін әкпен немесе әк сүтімен өңдеу нәтижесінде (2.1)-ші реакция бойынша тұнба түзіледі. Каустификациялау процесінде әк сүтінің орнына әкті қолдану:
1) СаО-ны сөндіру жылуын қолдануға және 2) әк сүтімен келетін суды процестен ығыстыру нәтижесінде күйдіргіш натрдың шоғырланған ерітіндісін алуға мүмкіндік береді. Сода ерітіндісін каустификациялау процесі кинетикалық аймақта жүретін, «сұйық-қатты» жүйесіндегі қайтымды экзотермиялық процесс болып табылады. Реакцияның нәтижесі негізінен еритін компоненттердің Са(ОН)2 мен СаСО3-ң ерігіштерінің қатынасына, яғни ОН- және СО32- иондарының ерітіндідегі концентрацияларына байланысты болады.
Процестің басында (2.1) реакциясының бағыты оң жаққа ығысқан, себебі СаСО3-ң ерігіштігі Са(ОН)2-ң ерігіштігінен төмен. Мысалы, 1000С-де Са(ОН)2-ң судағы ерігіштігі 0,07%, ал СаСО3-кі - 0,00002% ғана болады. Сонымен қатар, каустификация процесі басталғанда ерітіндінің құрамында көп мөлшерде СО32- иондары болады. Бұл иондар ерігіштігі онсыз да өте төмен СаСО3-тің ерігіштігін одан бетер төмендетеді. Каустификация барысында ерітіндіде ОН- иондары жиналады, ал СО32- иондарының мөлшері азаяды. Сондықтан СаСО3-тің ерігіштігі артады да, Са(ОН)2-ң ерігіштігі төмендейді. Тұздардың ерігіштігі бірдей болған кезде тепе-теңдік орнайды.
Қайтымды реакцияның (2.1) тепе-теңдік тұрақтысы жалпы түрде былай жазылады:
|
(2.2) |
Каустификация кезінде реакциялық қоспада әрдайым қатты күйде кальций гидрооксиді мен карбонаты болады, сондықтан олардың мәндері [Ca(OH)2] және [CaCO3] тұрақты және оларды тепе-теңдік тұрақтысының мәніне енгізуге болады, яғни:
|
(2.3) |
Сонда тепе-теңдік тұрақтысы:
|
(2.4) |
(2.4) теңдеуінен байқайтынымыз, қарастырылып отырған жүйеде тепе-теңдік тек қана кальций гидроксиді мен карбонатының ерігіштіктерінің қатынасымен анықталады. NaOH-тың тепе-теңдік шығымын каустификация дәрежесі (Х) деп атайды, оны өнімнің тәжірибе жүзінде алынған мөлшерінің оның теориялық алынуға қажет мөлшеріне қатынасымен анықтайды:
Х = Gтәж/ Gтеор |
(2.5) |
Бұл жерден NaOH-тың тепе-теңдік шығымын, яғни каустификация дәрежесін жоғарылату әдістерін анықтауға болады.
2.2 Сода ерітіндісінің каустификация дәрежесін жоғарылату тәсілдері
Тепе-теңдік каустификация
дәрежесі (яғни тепе-теңдік жағдайдағы
Na2CO3-тің NaOH-қа айналу дәрежесі)
бастапқы ерітіндідегі Na2CO3–тің концентрациясының
төмендеуімен жоғарылайды. Бұл жағдайда тепе-теңдік
каустификацияланған ерітіндіде [СО32-] иондарының концентрациясы
төмендейді және қатынасы жоғарылайды, яғни каустификация дәрежесі де
артады. Сонымен қатар, каустификацияланған ерітіндідегі судың
мөлшері артады, яғни оны буландыруға кететін будың да шығыны
жоғарылайды. Сондықтан, бастапқы ерітіндінің тиімді концентрациясын
таңдау кезінде тек каустификация дәрежесі ғана емес, сонымен қатар
алынатын NaOH ерітіндісінің концентрациясы да ескеріледі.
Тәжірибелік жағдайда Na2CO3-тің 2-3н-ді ерітіндісі (яғни
10-15%-ды ерітіндісі) қолданылады. Бұл кезде каустификация дәрежесі
шамамен 90% болады және алынған өнімдегі NaOH-тың концентрациясы
100-120г/дм3
құрайды.
Буландыруға жіберілетін өнімдік ерітіндідегі NaOH-тың төмен
концентрациясы - әктік әдістің негізгі
кемшілігі болып
саналады.
Температураның каустификация дәрежесіне әсері біркелкі емес. Температураның жоғарылауы экзотермиялық реакцияның тепе-теңдігін кері бағытқа ығыстырады, СаСО3-тің ерігіштігінің жоғарылауының әсерінен тепе-теңдік тұрақтысы және каустификация дәрежесі төмендейді. Бірақ, температураның жоғарылауы кинетикалық аймақта жүретін (2.І)-ші әртекті реакцияның жылдамдығын арттырады. Сонымен қатар, температураның жоғарылауымен кальций карбонатының тұну жылдамдығы жоғарылайды, яғни кальций карбонаты ірі кристалды тұнба түзеді. Ірі кристалдар тұнбаға тез тұнады және тұнбадағы NaOH пен Na2CO3-ң қалдықтарын жуып шығару үшін қолданылатын судың шығыны да аз болады. Сондықтан каустификацияны жоғары температурада 80-900С-де каустификатор-реакторларда жүргізеді. Олар өткір бумен немесе ішінен бу жіберілетін түтікшелердің көмегімен қыздырылады. Каустификатордан шығарылатын суспензия тұндырғыштарға беріледі. Тұндырғыштан кейін ерітінді декантацияланып (ерітіндіні қатты бөлшектерден айыру), үшқорапты вакуум-буландыру қондырғысында буландырылып, балқытуға және қатты өнім алу сатысына жіберіледі. Қатты өнім қабықшалар немесе түйіршіктер түрінде өндіріледі. Күйдіргіш натрды толық бөліп алу үшін шлам (тұнба) шаюшы-декантер аппараттарында көп сатылы шайылады. Мөлдірленген ерітінді декантердің жоғарғы жағынан шығарылып буландыру бөліміне жіберіледі. Жуылған шлам (тұнба) барабан вакуум-сүзгіштерде бөлініп қалдық жинағыштарға жіберіледі.
3 Қондырғының сипаттамасы және жұмысты орындау әдістемесі
3.1. Қондырғылар, техникалық және аспаптық құралдар:
1. Каустификацияға арналған зертханалық қондырғы
2. Химиялық ыдыстар
3. Титрлеу қондырғысы
4. Liston А 1210 аквадистилляторы
5. ВЛТЭ-150 зертханалық таразысы
6. Вакуум-сүзгіш қондырғы
3.2 Қондырғының сипаттамасы
Сода ерітіндісін каустификациялауға арналған зертханалық қондырғының сызба-нұсқасы 2.1-ші суретте көрсетілген. Ол сумен толтырылған термостаттан (1), суды жылытуға арналған электр қыздырғыштардан (2) және араластырғыштан (4) тұрады. Термостаттағы температураны қосалқы термометрмен (7) қадағалап, автоматты бағыттаушы жүйеге жалғанған кедергілік термометрдің (3) көмегімен реттейді. Термостаттың ішіне қақпағы бар фарфор стакан түрінде жасалған каустификатор (5) орналастырылған, оның қақпағының тесігі арқылы араластырғыш (6) өткізілген.
3.3 Каустификацияға қажетті әк тасының шығынын есептеу
1. Тәжірибе жүргізу үшін бастапқы сода ерітіндісінің концентрациясы
5-20% аралығында болатын үш ерітінді алады. 200С-де концентрациясы 22%-дан жоғары болатын ерітінді дайындау мүмкін емес, себебі мұндай концентрация Na2CO3-ң судағы ерігіштігінен жоғары болады.
2. Концентрациясы белгілі ерітіндінің берілген көлеміне (2.1)-ші реакция бойынша қажетті СаО-ң теориялық шығыны есептеледі. Ол үшін ең алдымен бастапқы ерітіндідегі Na2СО3-тің құрамын титрлеу арқылы анықтайды.
3. Талдау жүргізу үшін конусты колбаға зерттелетін ерітіндінің 10мл көлемін пипетканың көмегімен құйып, оған 40-50мл дистилденген су және 2-3тамшы метилқызғылт индикаторын қосып, 1н НСІ ерітіндісімен ерітіндінің түсі сарыдан әлсіз қызғылт түске енгенше титрлейді. Титрлеуге кеткен 1н НСІ-дың мөлшері (мл) Na2СО3-тің мөлшеріне эквивалентті болады.
Бастапқы сода ерітіндісінің құрамын есептеу мысалы. Бастапқы сода ерітіндісінің 10мл көлемін титрлеуге 20мл 1н НСІ ерітіндісі кетсін дейік. Бастапқы сода ерітіндісінің концентрациясын келесі формула бойынша есептейді:
|
(2.6) |
мұндағы: V – сынаманы титрлеуге шығындалған 1н тұз қышқылы ерітіндісінің көлемі, мл; Vсод – титрлеуге алынған сода ерітіндісі сынамасының көлемі, мл; К - 1н тұз қышқылы ерітіндісінің титрінің түзету коэффициенті (К=0,95); 53 - Na2CO3-тің г-эквиваленті. |
Сода ерітіндісінің концентрациясы:
|
Бастапқы ерітіндінің берілген (200мл) көлеміндегі Na2CO3-тің мөлшері:
|
4. Концентрациясы с (%) салмағы m (г) сода ерітіндісіне жұмсалатын СаО-ң шығын коэффициенті (b) келесі теңдеу бойынша есептеледі:
|
(2.7) |
мұндағы: 56 және 106 – сәйкесінше СаО мен Na2CO3-тің молярлық салмақтары. |
5. Стехиометриялық мөлшерден 5% артығымен алынған СаО-ң шығыны (а)
:
а=1,05 b |
(2.8) |
Зертханалық жағдайда каустификация дәрежесінің сода ерітіндісінің концентрациясына тәуелділігін анықтау мақсатымен каустификация жүргізу үшін майдаланған сөндірілмеген әк тасы мен сода ерітіндісінің үш түрлі концентрациясының 100 немесе 200 грамм мөлшері қолданылады.
3.4 Жұмысты орындау тәртібі
1. Фарфор стаканға (5) берілген мөлшердегі (100-200г) бастапқы сода ерітіндісін құйып, алдын-ала керекті температураға дейін қыздырылған термостатқа (1) орналастырады.
2. Ерітінді араластырғышы қосылған каустификаторда 800С-ге дейін қыздырылады, содан кейін ерітіндіге майдаланған әк тасын 5-10минут аралығында аз-аздап қосады.
3. Сода ерітіндісіне есептелген әк тасының барлығын қосып болғаннан кейін тәжірибенің басталу уақытын белгілейді. Каутификацияны
40-60минут аралығында жүргізеді. Каустификация температурасы тәжірибе барысында тұрақты 800С болуы керек.
4. Тәжірибе аяқталғаннан кейін араластырғышты тоқтатып, каустификаторды термостаттың ішінен алады. Каустификация дәрежесін анықтау үшін қалдықты 0,06МПа вакуумда сүзіп алу керек, ол үшін Бунзен колбасын және Бюхнер үрінкесін қолданады. Сүзіндіні конусты колбаға құйып алады. Тұнбаны ыстық сумен шайып, жуынды суларды жинайды.
5. Фильтраттағы және жуынды сулардағы NaOH пен Na2CO3-ң құрамын титрлеу арқылы анықтап, олардың қосындысын есептейді.
6. Алынған мәліметтер бойынша әрбір тәжірибе үшін каустификация дәрежесін (Х) есептейді. Ол NaOH-ң фильтрат пен тұнбадағы мөлшерінің NaOH пен Na2CO3-тің (NaOH-қа есептегенде) фильтрат пен тұнбадағы қосынды салмағына қатынасы бойынша есептеледі. Содан кейін каустификация дәрежесінің бастапқы сода ерітіндісінің концентра-циясына тәуелділік графигін салады да, қорытынды жасайды.
|
1-термостат; 2-қыздырғыш; 3-контактілік термометр; 4,6- араластырғыш; 5-каустификатор; 7-бақылаушы термометр; 8-әкті салуға арналған үріңке. 2.1 сурет - Сода ерітіндісін каустификациялауға арналған қондырғының сызба-нұсқасы. |
3.5 Виртуалды жұмысты орындау тәртібі
Зертханалық жұмыстың компьютерлік нұсқасы бірнеше кезеңнен тұрады. Ең алдымен студенттер процестің теориялық негіздерімен және виртуалды жұмысты орындау әдістемесімен танысады. Содан кейін жұмысты орындау үшін келесі тесттік сұрақтарға жауап береді:
1) Каустік соданы химиялық әдіспен алуда қолданылатын реагенттер.
2) Каустификацияға берілетін сода ерітіндісінің тиімді концентрациясы.
3) Сода ерітіндісін әк тасымен каустификациялау реакциясының теңдеуі.
4) Сода ерітіндісін әк сүтімен каустификациялау реакциясының теңдеуі.
5) Сода ерітіндісін каустификациялау температурасы.
6) Ерітіндідегі Na2CO3-тің құрамын анықтау үшін қолданылатын ерітінді және оның концентрациясы.
7) Каустификация нәтижесінде пайда болатын шлам (қалдық).
8) Сода ерітіндісін каустификациялау дәрежесі.
9) Суспензияны бөлу тәсілі.
10) Әк тасын енгізу тәсілі.
Дұрыс жауапты таңдап, оны (O’k) батырмасымен қабылдап келесі сұраққа көшеді. Ұсынылған 10 сұрақтың 10-на дұрыс жауап бергеннен кейін студент жұмысты орындауға рұқсат алады («жұмысты бастау» тетігі). Бұл шарт орындалмаған жағдайда қайтадан бағдарламаның басына көшіп, тест-рұқсат тапсыру керек.
Содан кейін студент каустификация процесін орындайды (2.2-ші сурет): сода ерітіндісінің оқытушы берген мөлшерін (100 немесе 200 грамм) және ерітіндінің 3 түрлі концентрациясын таңдайды. Егер концентрация дұрыс енгізілген болса, онда (2.1)-ші реакцияның теңдеуі бойынша әктің стехиометриялық шығын коэффициентін (b) және 5%-ды артық мөлшерін (a)-ны есептеп, алынған мәліметтерді сәйкесті ұяшықтарға енгізеді. Концентрациялар дұрыс емес енгізілгенде немесе (b) және (a) мәндері дұрыс есептелмеген жағдайда «қосу» батырмасын басқан кезде жіберілген қателер көрсетіледі, оларды дұрыстау керек. Барлық мәліметтер дұрыс енгізілген жағдайда ғана жұмысты орындауға көшуге болады.
Жұмысты орындау үшін «әкті енгізу», «қосу», «температура» және «таймер» деген процесті жедел реттеу батырмалары қолданылады. Сода ерітіндісін каустификациялау процесінің технологиялық ережесі бұзылған кезде де жіберілген қателер көрсетіледі. Егер студент үштен көп қате жіберсе «қанағаттанарсыз» деген баға алады да, жұмысты қайтадан тест-рұқсаттан бастайды. Егер каустификация дұрыс жүргізілген болса, студент «қосу», «өшіру» батырмаларының көмегімен суспензияны сүзу (2.3-ші сурет) және тұнбаны шаю (2.4-ші сурет) процестерін орындауға көшеді. Содан кейін сәйкесті ұяшықтарда алынған фильтраттың, тұнбаның және жуынды сулардың салмақтары көрсетіледі. Фильтраттағы және тұнбадағы NaOH-ң және Na2CO3-ң (NaOH-қа шаққанда) қосынды мөлшерінің мәндері бойынша студент каустификация дәрежесін есептеп, оның мәнін сәйкесті ұяшыққа енгізеді. Егер есептеу дұрыс жүргізілген болса, бағдарлама каустификация дәрежесінің сода ерітіндісінің концентрациясына тәуелділік графигін тұғызады, ал студент жұмыс бойынша қорытынды жасайды.
|
2.2 сурет - Виртуалды зертханалық жұмысты орындаудың 1-ші кезеңі |
Студенттің процестің теориялық негіздерін игеру дәрежесін бағалау үшін жұмысты қорғауға арналған 20 сұрақтан тұратын тесттік тапсырмалар ескерілген:
1) Каустік соданы әкті әдіспен алудың электрохимиялық әдіспен салыстырғандағы артықшылығы.
2) Ерітіндінің СаСО3 бойынша қанығуын төмендету үшін қолданылатын тәсіл.
3) Каустификацияны әк тасының 5-10%-ды артық мөлшерімен жүргізу не үшін қажет?
4) Каустік соданы химиялық әдіспен алудың кемшілігі.
5) Каустік соданы электрохимиялық әдіспен алудың кемшілігі.
6) Каустификацияны жоғары температурада жүргізу себебі.
7) Кинетикалық аймақта жүретін әртекті процестің қай сатысы жәй жүреді?
8) Кинетикалық аймақта жүретін процестің жылдамдығына температураның жоғарылауы қалай әсер етеді?
9) Сода ерітіндісінің концентрациясын жоғарылатқан кезде оның каутификациялау дәрежесі қалай өзгереді?
10) Кинетикалық аймақта жүретін процестің жылдамдығына қатты заттың дисперсиялығының жоғарылауы қалай әсер етеді?
11) Сода ерітіндісін каустификациялау үшін әкті қолданудың артықшылығы.
12) Сода ерітіндісін каустификациялау үшін әкті қолданудың артықшылығы.
13) Сода ерітіндісін каустификациялау қай аймақта жүреді?
14) Каустік соданы әкті әдіспен алудың кемшілігі.
15) Каустік соданы әкті әдіспен алудың кемшілігі.
16) Ерітіндідегі Na2CO3-ң концентрациясының төменгі шегін негіздеу.
17) Ерітіндідегі Na2CO3-ң концентрациясының төменгі шегін негіздеу.
18) Ерітіндідегі Na2CO3-ң концентрациясының төменгі шегін негіздеу.
19) Каустификацияны жоғары температурада жүргізуді негіздеу.
20) Өндірістік жағдайда бірінші каустификациядан кейін қай саты жүреді?
Тесттік тапсырмаларды табысты тапсырғаннан кейін студентке: 19-20 жауапқа – «өте жақсы», 17-18 жауапқа – «жақсы», 15-16 жауапқа «қанағаттанарлық» деген бағалар қойылады. Егер студент 15-тен кем сұраққа жауап берсе, жұмыс орындалмаған болып саналады және оны қайта орындау керек. Студентке виртуалды жұмысты орындағаны үшін баға қойған кезде каустификацияны, сүзуді және каустификация дәрежесін есептеуді жүргізген кезде жіберілген қателері ескеріледі.
3.6 Талдауды жүргізу әдістемесі
Фильтрат пен жуынды сулардан СаСО3-і бөліп алғаннан кейін, ерітіндідегі NaOH пен Na2CO3-ң құрамын карбонатты барий хлоридімен тұндыру әдісімен анықтайды. Бұл әдіс бойынша зерттелетін ерітіндінің екі сынамасын алады. Бірінші сынаманы жалпы сілтілікті (NaOH+Na2CO3) анықтау үшін метил қызғылт индикаторының қатысында тұз қышқылымен титрлейді, ал екінші сынаманы NaOH-тың құрамын анықтау үшін алдын-ала Na2CO3-ті барий хлоридімен тұндырып содан кейін фенолфталеиннің қатысында тұз қышқылымен титрлейді.
1. Каустификациядан және қалдықты бөліп алғаннан кейінгі фильтраттың талдауын, қалдықты сумен шаймай тұрып анықтайды. Алдымен фильтраттың көлемін (V1) өлшейді, содан кейін фильтраттың 10мл көлемін 200-250мл конусты колбаға құяды. Колбаға 50мл дистилденген су, 2-3тамшы метилқызғылт индикаторын қосып, 1н НСІ ерітіндісімен ерітіндінің түсі сарыдан әлсіз қызғылт түске енгенше титрлейді. Сынақты титрлеуге кеткен 1н НСІ-ң мөлшері (v1) жалпы сілтілікті көрсетеді.
Күйдіргіш натрдың құрамын анықтау үшін фильтраттың басқа сынамасын (10мл) көлемі 200-500мл конусты колбаға құяды. Содан кейін колбаға 50мл дистилденген су және барий хлоридінің ерітіндісінің артық мөлшерін қосады (BaCI2-нің 10%-ды ерітіндісінің 30мл-ін). Бұл кезде ерімейтін барий карбонаты және барий гидроксиді түзіледі:
Na2CO3+BaCl2=2NaCl+BaCO3↓ |
(2.9) |
||
2NaOH+BaCl2=2NaCl+Ba(OH)2 |
(2.10) |
||
|
|
|
|
|
2.3 сурет – Виртуалды жұмысты орындаудың 2-ші кезеңі - суспензияны сүзу. |
|
|
2.4 сурет - Жұмысты орындаудың 3-ші кезеңі – тұнбаны жуып-шаю. |
Карбонатты тұндырғаннан кейін сынамаға 2-3тамшы фенолфталеин қосып 1н НСІ ерітіндісімен титрлейді. Титрлеуге кеткен 1н НСІ ерітіндісінің көлемі v2 (мл) сынамадағы NaOH-тың мөлшеріне эквивалентті болады. Фильтраттағы NaOH пен Na2CO3-ң құрамын келесі формулалардың көмегімен есептейді:
|
(2.11) |
|
(2.12) |
мұндағы: 40 және 53 - NaOH пен Na2CO3-ң г-эквиваленті; К – 1н НСІ ерітіндісінің түзету коэффициенті; 10 – фильтрат сынамасының көлемі, мл. |
2. Жуынды сулардың талдауы фильтраттың талдауына ұқсас болады, бірақ талдау барысында тұз қышқылының 1н ерітіндісінің орнына оның 0,1н ерітіндісі қолданылады. Жуынды сулардың көлемін анықтайды, әрқайсысы 20мл екі сынама алып, бірінші сынамадағы жалпы сілтілікті, ал екінші сынамадағы NaOH құрамын анықтайды.
-
Процестің технологиялық көрсеткіштерін есептеу
Каустік соданы химиялық әдіспен алу процесінің нәтижелігін сипаттайтын негізгі көрсеткіш болып каустификация дәрежесі саналады. Оны анықтау үшін (2.5) формуласы бойынша фильтрат пен тұнбадағы NaOH-ң салмағын және NaOH пен Na2CO3-ң қосынды салмағын (NaOH-қа шаққандағы) есептейді.
Каустификация дәрежесін есептеу мысалы
10мл фильтратты метилқызғылт қатысында титрлеуге 25мл (v1), ал осы фильтраттың 10мл-ін ВаСІ2 ерітіндісімен карбонатты тұндырғаннан кейін титрлеуге 21мл (v2) 1н НСІ ерітіндісі (К=0,95) кетті дейік. NaOH пен Na2CO3-ң концентрацияларын (2.11) және (2.12) формулалары бойынша есептегенде:
|
Каустификациядан кейін алынған фильтраттың барлық көлеміндегі (мысалы, фильтраттың жалпы көлемі V1=300мл) NaOH пен NaCO3-тің мөлшері:
|
Жуынды сулардың көлемі V2=200мл. Оның жалпы сілтілігін анықтау мақсатымен 20мл көлемін титрлеуге 0,1н НСІ ерітіндісінің 22мл (v1΄) кетті. Жуынды сулардағы (сынаманың көлемі 20мл) NaOH-ң құрамын анықтауға 18мл 0,1н НСІ ерітіндісі (v2) кетті. NaOH пен Na2CO3-ң концентрацияларын (2.11) және (2.12) формулалары бойынша есептегенде:
|
Алынған жуынды сулардағы NaOH пен NaCO3-тің жалпы мөлшері:
|
Каустификация процесінің нәтижесінде алынған NaOH-тың жалпы мөлшері 23,94+0,72=24,66г. Қалған соданың мөлшері 6.04+0,21=6,25г. немесе NaOH-қа есептегенде – 6,25х80/106=4,72г.
Сода ерітіндісінің каустификация дәрежесі (Х):
|
Талдау және есептеу нәтижелерін 2.1 және 2.2-ші кестелерге енгізеді.
2.1 - кесте Фильтратты талдау нәтижелері
Бастапқы ерітінді |
1н HCl ерітіндісінің көлемі, мл |
Фильтратты талдау |
|||||||
Көлемі V, мл |
Na2CO3-ң құрамы |
Көлем V1, мл |
Na2CO3-ң құрамы |
NaOH-ң құрамы |
|||||
г/л |
г |
v1 |
v2 |
г/л |
г |
г/л |
г |
||
|
|
|
|
|
|
|
|
|
|
2.2 - кесте Жуынды суларды талдау нәтижелері
Сода ерітіндісіндегі Na2CO3-ң құрамы, г/л |
0,1н HCl ерітіндісінің көлемі, мл |
Жуынды суларды талдау |
Каусти-фикация дәрежесі (Х), % |
|||||
Көлем V2, мл |
Na2CO3-ң құрамы |
NaOH-ң құрамы |
||||||
v1΄ |
v2΄ |
г/л |
г |
г/л |
г |
|||
|
|
|
|
|
|
|
|
|
:№3 ЗЕРТХАНАЛЫҚ ЖҰМЫС
МЕТАЛДАРДЫ ЭЛЕКТРОХИМИЯЛЫҚ МЫСТАУ
1. Жұмыс мақсаты:
1) Металдарды электрохимиялық (гальваникалық) қаптау процестерімен тәжірибе жүзінде танысу;
2) Металдарды электрохимиялық қаптау процесінің технологиялық көрсеткіштерін есептеу әдістерін игеру.
3) Процестің параметрлерінің электрохимиялық мыстау нәтижелігіне әсерін анықтау.
2 Теориялық мәліметтер
2.1 Электрохимиялық процестердің негіздері
Электрохимиялық процестер дегеніміз электр энергиясын химиялык энергияға немесе химиялық энергияны электр энергиясына айналдыру процестері. Электрохимиялық процестердің негізін Фарадей заңдары құрайды.
Фарадейдің бірінші заңына байланысты қандай да электродты процесс үшін электролиз кезінде алынатын заттың мөлшері ток күшіне және оның өту уақытына пропорционал, яғни электролиз кезінде бөлінетін заттардың мөлшері электролиттен өткен электр тоғының мөлшеріне тура пропорционал.
Фарадейдің екінші заңы иондардың табиғатының әсерін сипаттайды. Бұл заң бойынша әр түрлі электролиттер арқылы бірдей электр мөлшерін өткізген кезде электродтарда бөлінетін заттардың мөлшерлері олардың электрохимиялық эквиваленттеріне пропорционал болады.
Қандай да бір заттың 1грамм-эквивалент мөлшерін алу үшін электролит арқылы 96500К немесе 26,8а-с электр тогын өткізу кажет. Жанама реакциялардың жүруіне байланысты электролиз кезінде өндірілген заттың мөлшері Фарадей заңы бойынша өндірілуге қажет мөлшерінен әрқашан да кем болады. Электролиз кезінде электр энергиясын тиімді қолдану көрсеткіштері ретінде ток бойынша шығым және энергияның колдану дәрежесі қолданылады.
Ток бойынша шығым (ŋ) дегеніміз электролиз кезінде алынган заттың мөлшерінің (Gтәж) электр тогының бірдей шығыны кезінде Фарадей заңы бойынша алынуға қажет теориялық мөлшеріне (Gтеор) қатынасы:
|
(3.1) |
«Ток бойынша шығым» деген түсінік химиялық процестердегі өнімнің шығымы деген түсінікке сәйкес келеді. Заттың теориялық мөлшерін Фарадейдің екі заңын біріктіретін теңдеу арқылы есептеуге болады:
|
(3.2) |
мұндағы:
τ - электролиздің ұзақтығы, сағ; n – катионның валенттілігі; F - Фарадей саны, 26,8 а-сағ/г.-экв. |
Энергияны қолдану дәрежесі (μ) өнімнің бірлігін өндіруге қажет энергияның теориялық мөлшерінің (Wтеор) оның тәжірибе жүзінде жұмсалған мөлшеріне (Wтәж) қатынасымен анықталады:
|
(3.3) |
Өнімнің бірлігін өндіруге қажет энергияның теориялық шығыны (квт-сағ.) мына формуламен анықталады:
|
(3.4) |
мұндағы: Uтеор - ыдыраудың теориялық кернеуі, в. |
Uтеор=aт- кт |
(3.5) |
мұндағы: aт және кт – анодты және катодты реакциялардағы тең әсерлі потенциалдар, в. |
Энергияның тәжірибе жүзіндегі шығыны электролизердегі нақты кернеуге байланысты болады:
|
(3.6) |
Осы теңдеулерді түрлендіре отырып мынадай формула аламыз:
|
(3.7) |
Бұл теңдеуден энергияны қолдану дәрежесі ток бойынша шығымға тура пропорционал, ал электролизердегі нақты кернеуге кері пропорционал екенін көруге болады.
2.2 Металдарды электрохимиялық қаптау процестері
Өндірісте сулы ерітінділер мен балқымалардың электролизі кеңінен қолданылады. Өндірістің электрохимиялық әдістерінің химиялық әдістермен салыстырғандағы артықшылықтары: 1) технологиялық процестің жеңілдігі; 2) шикізат пен энергияның толық қолданылуы; 3) өндірілетін өнімнің жоғары сапасы. Көрсетілген артықшылықтарына байланысты электрохимиялық процестер көптеген өнімдерді өндіру үшін қолданылады (мысалы хлор, сілтілер, оттегі және т.с.с. өндірістерінде, металдарды және оларды қорғау қабықшаларын алғанда).
Металдарды коррозиядан қорғау үшін гальваникалық қаптау кеңінен қолданылады. Гальваникалық қаптауды сәйкес тұздардың сулы ерітінділерін электролиздеу арқылы түрлі-түсті металдарды бұйымның бетіне тұндыру арқылы алады.
Гальваникалық қаптаулар халықшаруашылығының көптеген салаларында кеңінен қолданылады. Олар металдарды коррозиядан қорғау үшін ғана емес, сонымен қатар негізгі бұйымның тозуға төзімділігін, электр өткізгіштігін және т.б. маңызды қасиеттерін жоғарылату үшін де қолданылады.
Бұйымдарды техникалық сипаттамаларына қойылатын талаптарды ескере отырып гальваникалық қаптауларды үш түрге бөлуге болады:
-
қорғау-тұтынушылық гальваникалық қаптаулар, олар бұйымның
бетін коррозиядан қорғаумен қатар оның тұтынушылық қасиеттерін жоғарылатады;
-
қорғаушы электролиздік қаптаулар бұйымдарды әртүрлі
агрессивтік ортада коррозиядан қорғау үшін, көлік, ұшақтар, радиотехника және электроника өнеркәсіптерінде, құрылыста қолданылады;
-
арнайы гальваникалық қаптаулар металдың бетіне арнайы белгілі
қасиеттер беру үшін қолданылады (мысалы, беріктік, төзімділік, магниттік, электрқорғаушы). Сонымен қатар арнайы гальваникалық қаптаулар тозған бұйымдарды қалпына келтіру үшін де қолданылады.
Металдарды электрохимиялық қаптау процестерінің ең көп тараған түрлеріне никельдеу, хромдау және мырыштау жатады. Мырыштау бұйымды тікелей қаптау үшін қолданылады. Никельдеу процесі кеуектілігі төмен темірлерді қаптау үшін ғана қолданылады. Бұйымдардың кеуектілігін төмендету үшін алдымен оны мыспен, содан кейін никельмен қаптайды. Хром да темірдің бетінде кеуекті қабат түзетіндіктен, темірді алдын-ала никельдеп, содан соң хромдайды. Жоғарғы нәтиже алу үшін темірдің бетін төрт қабатпен қаптау керек: никельмен, мыспен, екінші қайтара никельмен және хроммен.
Химиялық және электрохимиялық қасиеттеріне байланысты мысты қаптаулар жеке қолданылмайды. Мыс атмосферады тез тотығып бұйымның бетінде оксидтер мен негізгі тұздар түзеді. Мысты тікелей болаттың бетіне тұндыруға болмайды, себебі болат күкірт қышқылында ериді. Сондықтан мысты қаптаулар никельдеу және хромдаудың алдында жүргізіледі, бұл қымбат және тапшы никельді үнемдеуге мүмкіндік береді. Темірді көміртекпен цементтеу процесінде мыс жеке қаптаушы ретінде қолданылып, бұйымның цементтелмейтін бөліктерін коррозиядан қорғайды. Баспа табақшаларының өндірісінде мыс негізгі жұқа қабат ретінде қолданылады.
Қорғау әрекетінің механизміне байланысты барлық гальваникалық қаптаулар анодты және катодты болып бөлінеді. Егер қаптаушы металдың электродты потенциалы қапталатын металдың электродты потенциалынан аз болса (яғни, егер қаптаушы металдың электр терістігі көбірек болса), онда қаптау анодты болып, электролиттің әсерінен қаптаушы металл ериді. Болатқа қатысты мырыш пен кадмий анодты қаптаушы болып табылады. Ал мыс, хром, никель, қалайы, қорғасын, алтын және күміс катодты қаптаушы болады. Металдарды электрохимиялық жолмен қаптаған кезде қапталатын зат катод рөлін атқарады. Оған металл катиондары жұқа біркелкі қабат түрінде тұнады. Қаптаушы металл анод рөлін атқарады және электролитте ериді.
Никельдеу процесінде металды никель анод рөлін атқарады да, элетролиз процесінде ериді. Электролит ретінде құрамында 170-200г/л NiSO47H2O болатын никель сульфатының ерітіндісі қолданылады. Ерітіндінің электр өткізгіштігін жоғарылату үшін оған 80-160г/л Na2SO410H2O, 20г/л NaCl, 20г/л Н3ВО3 қосады. Никельдеу процесінде электродтарда келесі процестер жүреді. Болат катодта никель немесе сутегі бөлінуі мүмкін:
Ni2++2e=Ni0 |
(3.8) |
2H++2e=H2 |
(3.9) |
|
|
Ni2+ ионының разрядталуының тең әсерлі потенциалы (φNi = – 0,23в) H+ ионының разрядталуының тең әсерлі потенциалынан (φН2 = – 0,415в) аз болғандықтан, катодта тек қана металды никель бөлінеді. Анодта тотығу-тотықсыздану реакциялары жүреді:
Ni0 –2е= Ni2+ |
(3.10) |
2OH-–2ē=H2O+0,5O2 |
(3.11) |
|
|
Бұл кезде никельді анодтың еруі басымырақ болады.
Мыстау процесінде қышқыл электролиттер қолданылады, олардың құрамында 200-250г/л мыс купоросы (CuSO45H2O) және 50-70г/л күкірт қышқылы (H2SO4) болады. Анод ретінде мыс табақшалары, ал катод ретінде никель немесе никельденген болат бұйым қолданылады. Мыстың электродты потенциалының мәні (φCu=+0,34в) оң таңбалы болғандықтан, катодта сутегі тотықсызданбайды. Сондықтан еківалентті мыс иондары катодта разрядталады:
Cu2+ +2e=Cu0 |
(3.12) |
Анодта (никельдеу процесіне ұқсас) мыс анодының ерітіндіде еруі жүреді:
Cu0–2e=Cu2+ |
(3.13) |
|
|
Бұл шарттарда мыстың ток бойынша шығымы 100%-ды құрайды.
Хромдау процесінде катод рөлін хромдалатын темір бұйым, ал электролит ретінде хромқышқылының ерітіндісі қолданылады. Электролиз процесінде темір катодта алты валентті хромның металды хромға немесе молекулалы сутегіге дейін тотықсыздануы жүреді:
СrО4-2+6ē+4Н2О=Сrº+8ОН |
(3.14) |
2Н++2ē=Н2 |
(3.15) |
Ал анодта келесі реакциялар жүреді:
2ОН-–2ēН2О+0,5О2 |
(3.16) |
Сr+3–3ēCr+6 |
(3.17) |
Хромдау процесінде ток бойынша шығым өте төмен болады (алты валентті хромға есептегенде 8-16%). Электр энергиясының негізгі бөлігі жанама процестерге жұмсалады:
СrО4+3+4ē+4Н2ОСr(ОН)2+6ОН- (катодты процесс) |
(3.18) |
Сr+3–3ēСr+6 (анодты процесс) |
(3.19) |
Хромның сапалы тұнбаларын алу үшін электролиттің құрамында міндетті түрде күкірт қышқылы немесе оның тұздары болуы керек. Күкірт қышқылы хромдау кезінде пайда болатын коллоидты қабықшаны ыдыратады.
3 Қондырғының сипаттамасы және жұмысты орындау әдістемесі
3.1 Қондырғылар, техникалық және аспаптық құралдар:
1. Металдарды электрохимиялық қаптау қондырғысы
2. ВЛТЭ-150 зертханалық таразысы
3. ШС-80 кептіру шкафы
3.2 Қондырғының сипаттамасы
Электрохимиялық қаптауға арналған қондырғының сызба-нұсқасы 3.1-ші суретте көрсетілген. Ол анодпен (5) және катодпен (6) жабдықталған электролизерден (4), вольтметрден (7), кулонометрден (3) және реостаттан (3) тұрады. Электролизер ретінде сыйымдылығы шамамен 1л шыны ыдыс қолданылады. Анод ретінде электролизердің қақпағына мықтап бекітілген екі жез немесе мыс табақшалары қолданылады. Катод ретінде никельденген бұйым немесе никель табақшасы қолданылады.
|
1-тұрақты ток көзі; 2- реостат; 3- кулонометр; 4- электролизер; 5-анод; 6-катод; 7-вольтметр; 8-амперметр; 9-өшіргіш. 3.1 сурет - Электролизге арналған зертханалық қондырғының сызба-нұсқасы |
3.3 Жұмысты орындау тәртібі
1. Бұйымды электролизге дайындау.
Бұйымның бетінің тегіс еместігі, лай, тот, майлы дақтар қапталу сапасын және электролиз процесін нашарлатады. Сондықтан қапталатын бұйымдарды алдын-ала мұқият тазарту қажет. Темір бұйымның бетін механикалық және химиялық әдістермен тазартады. Механикалық әдістерде зімпара қағазы немесе киіз қолданылады. Бұйымдардың бетін жылтырату үшін хромды немесе крокусты пасталар қолданылады. Бұйымдарды майсыздандыру және су сіңірімділік қабілетін жоғарылату үшін оларды концентрациясы 100г/л NaOH ыстық сілтілік ерітіндісімен немесе органикалық ерітінділермен (мысалы, этанолмен) өңдейді.
2. Темір бұйымды электролизерге салар алдында сумен жақсылап шайып, кептіріп, салмағын техникалық таразыда 0,01г дәлдіктеп өлшеп алады.
3. Мыстау процесін жүргізу үшін 3.1-ші суретте көрсетілгендей етіп зертханалық қондырғыны жинайды. Электролизерді келесі құрамдағы электролитпен толтырады: CuSO45H2O – 250г/л, H2SO4 – 50г/л. Электрод табақшаларының ұзындығының 3/4 бөлігі электролитке батып тұруы керек.
4. Дайындалған қапталатын бұйымды катодтың орнына іліп, электролитке батырады. Электр тогын қосып, реостаттың көмегімен берілген ток күшін орнатады. Аспаптардың көрсеткіштері бойынша ток күшінің және кернеудің мәндерін жазып алады.
5. Электролиз процесін 5-10минут аралығында жүргізеді. Мыстау процесі аяқталғаннан кейін электр тогын өшіріп, бұйымды электролизерден алып, кептіріп, салмағын аналитикалық таразыда 0,01г дәлдікпен өлшейді. Бұйымның қапталған ауданын анықтайды.
6. Электрохимиялық процестің негізгі көрсеткіштерін есептейді (металдың орташа қапталу қалыңдығы мен ток бойынша шығым).
Процестің технологиялық шарттары (процестің ұзақтығы, ток күші, орташа қапталу қалыңдығы, катодтың қапталу ауданы) оқытушының тапсырмасына сай әртүрлі болуы мүмкін. Процестің параметрлерін өзгерте отырып олардың электрохимиялық процестің көрсеткіштеріне әсерін анықтайды және процестің нәтижелігі бойынша қорытынды жасайды.
4 Электрохимиялық процестің көрсеткіштерін есептеу
Металдың қапталу қалыңдығын есептеу
Мыс қабатының орташа қапталу қалыңдығын δорт, (мкм) келесі формула бойынша есептейді:
δорт
= (3.20)
мұндағы: Gтәж – бұйымның қаптауға дейінгі (G1) және кейінгі (G2) салмақтарының айырмасы (Gтәж = G2 - G1), г; S – бұйымның мысталған ауданы, см2; - қаптайтын металдың тығыздығы (Cu= 8,95 г/см3), г/см3.
4.2 Ток бойынша шығымды есептеу
Ток бойынша шығым (3.1) формула бойынша есептеледі, мұндағы Gтәж – мыстың катодта тұнған салмағы, г; Gтеор – берілген шарттарда мыстың катодта тұнуға қажет теориялық мөлшері, г. Тұнған металдың теориялық мөлшері Фарадей заңдарына сәйкес (3.2) формула бойынша есептеледі.
Алынған тәжірибелік мәліметтер мен есептеу нәтижелерін 3.1-ші кестеге енгізеді.
3.1 кесте - Электрохимиялық мыстау процесінің көрсеткіштері
Катодтың салмағы, г |
Мыстың катодта тұнған салмағы Gтәж, г |
Ток күші, а |
Катодтың электрлитке батырыл- ған ауданы, см2 |
Электро- лиз уақыты, сағ |
Қапталу қалыңды-ғы δорт, мкм |
Ток бойынша шығым ŋ, % |
|
Электролизге дейін G1 |
Электро лизден кейін G2 |
||||||
|
|
|
|
|
|
|
|
№4 ЗЕРТХАНАЛЫҚ ЖҰМЫС
ҚАТТЫ ОТЫНДЫ ТЕХНИКАЛЫҚ ТАЛДАУ
1. Жұмыс мақсаты:
-
Қатты отынның құрамындағы ылғалдылықты, күлділікті және ұшпа заттарды анықтаудың стандартты тәсілдерімен танысу.
2) Қатты отынның сапасын анықтау.
2 Теориялық мәліметтер
2.1 Отын-энергетикалық қорларының жалпы сипаттамасы
Отын-энергетикалық қорлар отындық және отындық емес, қалпына келетін және қалпына келмейтін, бірінші реттік және екінші реттік болып бөлінеді. Отындық қорларға жанғыш қазбалар (көмір, мұнай, торф, сланец және табиғи газ) жатады. Отындық емес қорларға атомдық және термоядролық энергия, күн энергиясы, гидроэнергия (өзендер энергиясы), жер қойнауының жылу энергиясы (геотермалдық), мұхит суының көтерілу және төмендеу энергиясы, жел энергиясы жатады. Қалпына келетін энергия көздеріне барлық отындық емес энергия көздері (атомдық энергиядан басқасы) және биомасса (ағаш және басқа да өсімдік шикізаттары) жатады. Қалпына келмейтін энергия қорларына өндірген сайын азая беретін энергия қорлары жатады. Олардың қатарына барлық жанғыш қазбалар мен атомдық "отын" - уран кіреді. Жоғарыда аталған барлық энергия көздері бірінші реттік болып саналады.
Екінші реттік энергия қорларына химия-технологиялық процесте пайда болатын соңғы, жанама және аралық өнімдердің энергетикалық потенциалдарының энергиялары жатады. Екінші реттік энергия қорларын қолдану арқылы өндірісті жартылай немесе толық энергиямен қамтамасыз етуге болады.
Отын дегеніміз жылу энергиясының көзі және химиялық өнеркәсіптің шикізаты болып саналатын табиғи немесе жасанды жанғыш органикалық заттар. Отынды агрегаттық күйі бойынша қатты, сұйық және газ тәрізді, ал пайда болуына байланысты табиғи және жасанды деп бөледі. Табиғи отындар: қаттылар - қоңыр және тас көмірлер, ағаштар, жанғыш сланецтер және шым тезек; сүйықтар - мұнай; газдар - табиғи газ және мүнай өндірісінің жолшыбай газдары. Жасанды отындар - табиғи отындарды өңдеуден пайда болған заттар: қаттылар - кокс, жартылай кокс, шым тезек және көмір брикеттері, ағаш көмірі; сүйықтар - бензин, керосин және басқа да мүнай өндеу нәтижесінде пайда болған сұйық өнімдер; газдар - генератор газы, кокстеу газы, жартылай кокстеу газы, мұнай өндеудің көмірсутекті өнімдері, сутегі.
Отын энергетикалық және технологиялық болып бөлінеді. Энергетикалық отынды электр және жылу энергиясын алу үшін жылу энергия станцияларында (ЖЭС-да) және қазандықтарда қолданады. Технологиялық отын тікелей технологиялық процестер мен операциялар жүргізілетін өндірістік қондырғыларда қолданылады (мысалы қатты отынды кокстеу және газдандыру процестерінде, шойын мен болат қорытуда, силикатты материалдарды күйдіруде, кептіру, буландыру, термиялық өндеу және т.б. процестерде).
Отынның негізгі технологиялық сипаттамалары ретінде оның жану жылуы (жылу бөлу қабілеті) және энергия сыйымдылығы қолданылады.
Отынның жылу бөлу қабілеті (жану жылуы) дегеніміз қатты немесе сұйық отынның салмақ бірлігінің (МДж/кг) немесе газ тәрізді отынның көлем бірлігінің (МДж/м3) толық жанып және жану заттары қалыпты температураға дейін салқындағанда бөлінетін жылудың жалпы мөлшері.
Отынның энергия сыйымдылығы дегеніміз отынның көлем немесе салмақ бірлігіндегі потенциалдық жылу энергиясының мөлщері. Отындардың сапасын салыстыру үшін отынның шығынын шартты отынның шығынымен салыстырады. Шартты отын ретінде 1кг жанғанда 29,3МДж энергия бөлетін отын саналады, оған қатысты көмірдің үлестік энергия сыйымдылығы орташа есеппен 33,5МДж/кг құрайды. Мұнай мен табиғи газдың энергия сыйымдылығы сәйкесінше шамамен 41,9 және 46,1МДж/кг құрайды, яғни салыстырып қарағанда жоғары болады. Сутегінің энергия сыйымдылығы (120,6МДж/кг) мұнаймен салыстырған үш есе жоғары, экологиялық таза отын болып саналады.
2.2 Қатты отынның химиялық құрамы
Қатты отын жанатын органикалық және жанбайтын бейорганикалық бөліктерден тұрады. Қатты отынның жанбайтын бейорганикалық бөлігін балласт деп атайды, оның құрамына минералды заттар мен су кіреді. Балласты заттар отынның жанатын бөлігін азайтады, соның әсерінен оның энергия сыйымдылығы төмендейді және отынды тасымалдау шығындары жоғарылайды. Отынның жанатын органикалық бөлігі көміртегі, сутегі, оттегі, азот және күкірттен тұратын өте күрделі зат. Күкірт отындағы зиянды қоспа болып саналады, өйткені ол жанған кезде күкірт диоксидіне айналып атмосфераны улайды. Күкірт отынның органикалық және минералды бөліктерінің де құрамына кіреді. Сульфатты күкірт күлдің құрамына өзгеріссіз өтеді.
Қатты отынның техникалық талдауы оның құрамы мен техникалық құндылығы жөнінде алғашқы жобалы мәліметтер береді. Әдетте техникалық талдау отынның ылғалдылығын (W), күлділігін (А), ұшпа заттардың бөлінуін (V), күкірттің мөлшерін және жылубөлу қабілетін (Q) анықтаудан тұрады.
Көмірдің құрамындағы ылғалдылық сыртқы, гигроскопиялық және химиялық байланысқан болып бөлінеді. Сыртқы ылғалдылық көмірдің түйіршіктерін жұқа қабықша түрінде қаптап тұрады және отынды 70-750С-де ауалы-құрғақ жағдайға кептіргенде ұшып кетеді. Гигроскопиялық ылғалдылықты көмір қоршаған ортадан сіңіреді, оның мөлшері ортаның салыстырмалы ылғалдылығына және температурасына байланысты болады. Көмірдегі гигроскопиялық ылғалдылықты шығару үшін отынды 1050С-де кептіреді. Химиялық байланысқан ылғалдылық көмір мен оның ішіндегі минералдық қоспалардың құрамында кристалдық су түрінде болады және ішкі немесе конституциялық деп аталады. Ол тек қана жоғары температурада көмірдің кристалдық торының бұзылуы нәтижесінде ғана шығарылады.
Көмірдегі ылғалдылықтың мөлшері әртүрлі болады (мысалы, тас көмірде 3-10%, ал қоңыр көмірде 30-40%). Отынның ылғалдылығы оның құрамындағы пайдалы заттардың құрамын және оның жылу беру қабілетін төмендетеді, оны тасымалдауға жұмсалатын шығындарды көбейтеді, көмірді байыту процесін қиындатады, сонымен қатар кокстеу жылдамдығын, яғни кокс пештерінің өнімділігін елеулі төмендетеді.
Отынның құрамындағы минералды қоспалар отынды жаққан кезде күл түзетіндіктен судан да зиянды қоспа болып саналады. Отынның минералдық бөлігін кальций, темір, магний, алюминий, натрий және басқа металдардың карбонаттары, силикаттары, сульфаттары, сульфиттері құрайды. Қатты отындарды жаққан кезде минералды заттар оксидтерге айналып қатты қалдық - күл түзеді. Күлділіктің мөлшерінің жоғары болуы отынды энергия көзі және химиялық шикізат ретінде қолдануды қиындатады. Күлділігі жоғары отындарды жаққан кезде пешті жиі тазарту қажет.
Көмірдегі бастапқы өсімдік заттарынан түзілген күлдің (көмірмен химиялық байланысқан конституциялық күл) және көмірге көміртүзу процесінде желмен, сумен енгізілген күлдің (енгізілген күл) қосындысын «ішкі күл» деп атайды. Көмірге әртүрлі қоспалар түрінде және оны өндіру кезінде енгізілген күлді «сыртқы күл» деп атайды. Отынның құрамындағы күлдің мөлшері әртүрлі болады: шым тезекте - 3-30%, сланцтер мен қоңыр көмірлерде - 50%-ға дейін, тас көмірлерде - 0,2-ден 30%-ға дейін. Антрациттердің құрамында күлдің мөлшері 5%-дан жоғары болмайды.
Ұшпа заттар дегеніміз отынды ауасыз ортада қыздырғанда түзілетін бу және газ тәрізді заттар. Ұшпа заттардың шығымы анықтауды жүргізу шарттарына (температура, қыздыру жылдамдығы, отынның бөлшектерінің өлшемдері, қондырғылардың құрылымдық сипаттамалары) байланысты болады. Әртүрлі отын түрлері үшін ұшпа заттардың шығымы да әртүрлі болады (антрациттерде 6%-ға дейін, тас көмірлерде 10-40%, қоңыр көмірлерде 45-55%, шым тезекте 70%-ға дейін). Ұшпа заттардың құрамына тас көмір шайыры және газдар (көміртек оксиді, сутегі, аммиак, метан, бензол, күкірт диоксиді) кіреді.
Қатты отынның техникалық талдауын жүргізген кезде оның құрамын абсолют құрғақ отынға қайта есептейді. Абсолют құрғақ отын дегеніміз зертханалық сынаманы 105-1100С-де тұрақты салмаққа дейін кептіргенде алынған отын. Абсолют құрғақ отынға қайта есептелген күлділік пен ұшпа заттардың мөлшерлерін Ааб және Vаб деп белгілейді.
3 Қондырғының сипаттамасы және жұмысты орындау әдістемесі
3.1 Қондырғылар, техникалық және аспаптық құралдар:
1. ШС-80 кептіру шкафы
2. SNOL 6,7/1300 муфель пеші
3. ВЛТЭ-150 зертханалық таразысы
4. Эксикатор
3.2 Қатты отынның ылғалдылығын анықтау әдістемесі
Отынның ылғалдылығын тікелей және жанама әдістермен анықтауға болады. Отынның ылғалдылығын тікелей салмақтық тәсілмен анықтау кезінде (МССТ 9616-60) отынның сынамасын инертті газ ағынында (әдетте азот) 105-1100С-де кептіреді, ал бөлінген су буларын хлор қышқылды магниймен немесе күкірт қышқылымен сіңіріп алады. Ылғалдылықты тікелей көлемдік тәсілмен анықтау кезінде (МССТ 9339-60) отынның сынамасын толуол қосып қыздырып, оның құрамындағы ылғалды толуолмен бірге айдап, содан кейін суды конденсациялап, көлемін өлшейді. Бұл тәсілдердің нәтижесінде өте дәл нәтижелер алынады, бірақ бұл тәсілдер салыстырып қарағанда күрделі болып саналады.
Қоңыр және тас көмірлердің, антрациттердің және жанғыш сланецтердің ылғалдылығын анықтау үшін жанама тәсіл қолданылады (МССТ 6379-59). Бұл тәсіл отынның сынамасын кептіру шкафында 105-110°С-де тұрақты салмаққа дейін кептіруге негізделген. Кептіру нәтижесінде отынның жоғалған салмағы ылғалдылық болып есептеледі.
Қатты отынның ылғалдылығын жанама тәсілмен анықтау тәртібі:
1. Көмірді ұнтақ күйге дейін майдалайды.
2. Алдын-ала салмағы таразыда өлшенген биіктігі 20-30 мм, диаметрі 35-40мм болатын шыны ыдысқа отынның 1грамын салып 0,01г дәлдікпен аналитикалық таразыда салмағын өлшейді. Ыдыстагы отынның қабатының қалыңдығы 5 мм-ден аспауы керек.
3. Отынның бөлшектерін жеңіл сілкіп тегістейді де, алдын-ала 105-1100С-ге дейін қыздырылған кептіру шкафында кептіреді. Кептіру кезінде ыдыстың қақпағы жартылай ашық болуы керек. Кептіру уақыты қоңыр көмірлер үшін - 90мин; антрациттер үшін -120мин; ал қалган отын түрлері үшін - 50-60мин.
4. Көрсетілгсн уақыт өткеннен кейін отын салынған ыдысты кептіру шкафынан алып, қақпағын толық жауып, алдымен ауада 2-3 мин., содан кейін эксикаторда бөлме температурасына дейін салқындатып, 0,001г дәлдікпен аналитикалық таразыда салмағын өлшейді.
5. Бақылау кептіруді 105-1100С-де 30мин аралығында жүргізеді. Егер салмақтың жоғалуы 0,01граммнан көп болса, онда кептіруді салмақтың азаюы 0,01г-нан аз болғанға дейін немесе көмірдің тотығуының нәтижесінде салмақтық көбеюі басталғанға дейін қайталайды. Көмірдің салмағы көбейген жағдайда есептеу үшін оның алдындағы салмақтың мәнін алады.
6. Зерттелетін отынның ылғалдылығын W (%) келесі формула бойынша есептейді:
W = |
(4.1) |
мұндағы:ΔG1 – кептіруден кейінгі отынның салмағының өзгеруі, г; ΔG1=G-G1; G – сыналатын отынның бастапқы салмағы, г; G1 – кептірілген отынның салмағы, г. |
3.3 Отынның күлділігін анықтау әдістемесі
Қатты отынның күлділігін анықтау үшін (МССТ 6382-52) отынның сынамасын жағып, алынған күлді тұрақты салмаққа дейін қыздыру керек: антрациттер, қоңыр және тас көмірлерді - 800±25°С-де, ал сланцтерді - 850±25°С-де. Сланцтерді талдаған кезде жоғары температураның қолданылуы олардың минералдық бөлігіндегі карбонаттарды ыдыратуға жоғары температураның қажеттілігімен түсіндіріледі.
Қатты отынның күлділігін анықтау тәртібі:
1. Алдын-ала салмағы аналитикалық таразыда өлшенген биіктігі 25-30мм және диаметрі 30мм фарфор тигелге 1г отынның сынамасын салып, салмағын аналитикалық таразыда 0,001г дәлдікпен өлшеп, 850±250С-ге дейін қыздырылған муфель пешіне салады.
2. Түзілген күлді қалдықты осы температурада 1,5сағат аралығында қыздырады. Содан кейін қысқыштың көмегімен тигелді муфель пешінен алып, алдымен ауада 5минут, содан кейін эксикаторда бөлме температурасына дейін салқындатады.
3. Салқындатылған тигелдің салмағын аналитикалық таразыда 0,001г дәлдікпен өлшейді.
4. Сенімді нәтижелер алу үшін күлді қалдықты соңғы екі өлшенген салмақтардың айырмашылығы 0,001г-нан аз болғанға дейін әр 30минут сайын қыздырады. Егер салмақ көбейсе, онда есептеу үшін оның алдындағы салмақтың мәнін алады.
5. Отынның күлділігін А (%) мына формула бойынша есептейді:
А= |
(4.2) |
мұндағы: G - отынның бастапқы салмағы, г; G2 - күлді қалдықтың салмағы, г. |
6. Отынның күлділігін абсолют құрғақ отынға (Ааб) қайта есептеу үшін төменде берілген формула қолданылады:
Ааб
= |
(4.3) |
3.4 Қатты отынның құрамындағы ұшпа заттарды анықтау әдістемесі
Көмірдегі ұшпа заттардың шығымын анықтау әдістемесі (МССТ 6382-65 сәйкесті) отынның сынамасын 850±25°С-де 7минут аралығында қыздырып, көмірдің жоғалтқан салмағын анықтауға негізделген.
Қатты отындағы ұшпа заттардың құрамын анықтау тәртібі:
1. Ылғалдылығы (W) белгілі отынның 1грамын биіктігі 40мм, диаметрі 30мм алдын-ала салмағы өлшенген фарфор тигелге салып, салмағын аналитикалық таразыда ±0,0001г дәлдікпен өлшейді.
2. Тигелдің қақпағын жеңіл жауып қояды. Ұшпа заттар қақпақтағы тесіктер арқылы шығады.
3. Муфель пешін алдын-ала 800±25°С-ге дейін қыздырады. Тигелді электр пешінің түбінен 10-20мм биіктікте тұратындай етіп орналастырады. Ол үшін ыстыққа төзімді тіреуіштер қолданылады. Температураны өлшеу үшін терможұп қолданылады. Терможұптың ыстық жағы пештің түбінен 10-20мм биіктікте тұруы керек.
4. Көмірді 7минут қыздырғаннан соң беті жабық тигелді қысқыштың көмегімен пештен алып, 3-5минут ауада, содан кейін эксикаторда бөлме температурасына дейін салқындатады.
5. Салқындатылған тигелдің салмағын аналитикалық таразыда 0,001г дәлдікпен өлшейді. Зерттелетін отындағы ұшпа заттардың V (%) құрамын келесі формуланың көмегімен есептейді:
Vaб
= |
(4.4) |
мұндағы: G – отынның бастапқы салмағы, г; ΔG3 – қыздырудан кейінгі отынның салмағының өзгеруі, г; ΔG3= G-G3; G3 – отынның қыздырудан кейінгі салмағы, г; W – зерттелетін отындағы ылғалдылықтың құрамы, %. |
6. Алынған мәліметтер (отынның ылғалдылығы, күлділігі, ұшпа заттардың құрамы) бойынша отынның сапасы туралы қорытынды жасайды.
№5 ЗЕРТХАНАЛЫҚ ЖҰМЫС
СУДЫҢ САПАЛЫҚ КӨРСЕТКІШТЕРІН АНЫҚТАУ
1 Жұмыс мақсаты:
-
Судың кермектілігі мен тотығуын анықтаудың стандартты әдістерімен тәжірибе жүзінде танысу.
2) Әртүрлі сулардың сапасын анықтау.
2 Теориялық мәліметтер
Көптеген химия, металлургия, тамақ және жеңіл өнеркәсіптерінде, жылу электр станциялары (ЖЭС) мен атом электр станцияларында (АЭС) көп мөлшерде су қолданылады. Су өндірісте шикізат немесе реагент ретінде (мысалы, сутегі және оттегі өндіруде, күкірт және азот қышқылы, сода, күйдіргіш натр өндірістерінде, әртүрлі гидратация және гидролиз реакцияларында және т.б.); қатты, сұйық және газ тәрізді заттардың еріткіші ретінде; жылутасымалдағыш немесе салқындатқыш ретінде; газдарды және қатты материалдарды жуып-шаю үшін қолданылатын механикалық тазартушы ретінде; кендерді флотациялық және басқа да сулы әдістермен байытуда; қондырғылар мен аспаптарды тазартуда; гидравликалық, жылулық және атом электростанцияларында және т.б. қолданылады. Су буы немесе жылытылған су эндотермиялық процестердің жылдамдығын жоғарылату және жылудың шығынын толықтыру мақсатымен әрекеттесуші заттарды қыздыру үшін қолданылады.
Су қатты, сұйық және газ тәрізді заттардың жақсы еріткіші болғандықтан оның құрамында көптеген қоспалар кездеседі, сондықтан табиғи су үш түрге бөлінеді.
Атмосфералық су - бұл жаңбыр мен қар сулары. Олардың қүрамында қоспалар аз болады, негізінде оларға еріген газдар (СО2, О2, N2, шаң, H2S және т.б.), тұздар, бактериялар және т.б. жатады.
Жер бетіндегі суларға ашық жатқан су қоймаларындағы, өзендердегі, көлдердегі, теңіздердегі, мұхиттардағы сулар жатады. Бұл сулардың құрамына әртүрлі минералдық және органикалық қоспалар кіреді. Теңіз суының құрамында бағалы және радиоактивті металдармен қатар элементтер кестесіндегі барлық заттар кездеседі. Егер 1кг суда 1г-ға дейін тұз болса, онда ол тұщы су, 1г-нан 10г-ға дейін болса – тұздылау су, ал 10г-нан көп болса тұзды су деп аталады.
Жер асты суларына артезиан құбырларының, құдықтардың, бұлақтардың және гейзерлердің сулары жатады. Олардың құрамында еріген тұздар көп болады. Олардың тұздылығы жер қыртысының және тау жыныстарының құрылысына және құрамына байланысты болады. Жер қыртыстарының және тау жыныстарының сүзу қабілеті жер асты суларының жоғарғы мөлдірлігін және құрамында органикалық қосылыстардың болмауын қамтамасыз етеді.
Су адам тіршілігінде қолданылатындықтан оған қойылатын талаптар да өте қатаң болады. Судың сапасы оның мөлдірлігі, түсі, иісі, температурасы, жалпы тұздылығы, кермектілігі, тотығуы және судың реакциясы деген көрсеткіштермен сипатталады.
Судың тотығуы судың құрамында органикалық косылыстардың болуын сипаттайды және органикалық қосылыстарды тотықтыруға қажет калий перманганатының (мг) мөлшерімен анықталады. Судың тотығуының мөлшері әртүрлі болуы мүмкін. Жер бетіндегі сулардың жер асты суларымен салыстырғанда тотығуы жоғары болады. Судың тотығуының шекті рұқсат етілген концентрациясы (ШРҚ) 5,0-7,0мг/л құрайды.
Судың реакциясы дегеніміз судың қышқылдық және сілтілік дәрежелері. Ол сутегі иондарының концентрациясымен сипатталады және индикатордың көмегімен анықталады. Табиғи сулардың реакциясы бейтарапқа жақын болып келеді (рН=6,8-7,3), айналымдығы сулардың реакциясы өндірістің түріне байланысты болады. Егер рН<6,5 болса су қышқылдық, рН>7,5 болса - сілтілік деп аталады.
Жалпы тұздылық судың құрамындағы органикалық және минералдық қоспалармен сипатталады. Оның мөлшерін құрғақ қалдықтың салмағымен (мг/дм3) анықтайды. Ол үшін 1л суды буландырып, тығыз қалдықты 1100С-де тұрақты салмаққа дейін кептіріп, қалған қалдықтың салмағын таразыда өлшейді.
Көптеген өндірістерде судың негізгі сапалық көрсеткіші болып судың кермектілігі саналады. Судың кермектілігі судың құрамындағы кальций және магний түздарының мөлшерін көрсетеді. Құрамындағы Са2+ және Mg2+ иондарының мөлшеріне байланысты су үш түрге бөлінеді: Са2+ мен Mg2+ иондарының мөлшері 3мг-экв/дм3 дейін болса жұмсақ су; 3-тен 6мг экв/дм3 дейін - орташа кермекті су; 6мг-экв/дм3 жоғары болғанда - кермекті су деп аталады. Судың кермектілігі үш түрге бөлінеді:
Уақытша (карбонатты немесе жойылатын) кермектілік судың құрамындағы кальций және магний бикарбонаттарының (Са(НСО3)2; Mg(HCO3)2) мөлшерін көрсетеді. Олар суды қайнатқан кезде ерімейтін түрге айналып, қатты тұнба (қақ) түзеді:
Ca(HCO3)2 = CaCO3 ¯Ї+ H2O + CO2 |
(5.1) |
2Mg(HCO3)2 = MgCO3×Ч Mg(OH)2+ 3CO2 + H2O |
(5.2) |
Тұрақты (карбонатты емес) кермектілік судағы кальций мен магнийдің тұнба түзбейтін нитраттарының, хлоридтерінің, сульфаттарының мөлшерін көрсетеді.
Уақытша және тұрақты кермектіліктердің қосындысы жалпы кермектілік деп аталады.
Суды өндірісте қолдану алдында өндірістік талаптарға сай су дайындау шаралары жүзеге асырылады. Өндірісте қолданылатын судың құрамында: 1) реакцияға кері әсер ететін; 2) аппараттарды коррозияға ұшырататын және 3) аппараттар мен құбырлардың ішінде қақтар мен тұнбалар түзетін зиянды заттар болмауы керек. Судың құрамындағы қоспалар көбінесе ерітінділер, коллоидтық және механикалық жүзгін бөлшектер түрінде болады. Суды дайындаудың негізгі операцияларына тұндыру, құм немесе тас қабаты арқылы сүзу, бейтараптандыру, дегазациялау және залалсыздандыру жатады. Суды мөлдірлеу немесе коллоидты қоспалардан тазарту (коагуляциялау) процестерінде коагулянттар (Al(SO4)3, FeSO4, NaA102) қолданылады.
Суды жұмсарту дегеніміз оның құрамындағы кальций және магний тұздарын толық немесе жартылай ажырату. Суды дөрекі жұмсартуды (шамамен 0,3мг-экв/дм3-ге дейін) әк тасы, күйдіргіш натр немесе сода (әк-содалы әдіс) қосу арқылы жүзеге асырады:
Ca(HCO3)2 + Ca(OH)2 2CaCO3 + 2H2O |
(5.3) |
Mg(HCO3)2 + 2Ca(OH)2 2CaCO3 + Mg(OH)2 + 2H2O |
(5.4) |
CaSO4 + Na2CO3 CaCO3 + Na2SO4 |
(5.5) |
MgSO4 + Na2CO3 MgCO3 + Na2SO4 |
(5.6) |
MgCI2 + Na2CO3 MgCO3 + 2NaCl |
(5.7) |
|
|
Ең арзан және қол жетімді жұмсартқыш ретінде әк тасы немесе әк сүті саналады. Ал суды толық жұмсарту (0,03 мг-экв/дм3-ге дейін) үшін жұмсартушы реагент ретінде үшнатрийфосфаты (Na3PO4) қолданылады:
3Ca(HCO3)2 + 2Na3PO4 Ca3(PO4)2 + 6NaHCO3 |
(5.8) |
3MgCl2 + 2Na3PO4 Mg3 (PO4)2 + 6NaCl |
(5.9) |
|
|
Суды нәтижелі жұмсарту және тұссыздандыру үшін ионаламасу әдісін қолданған өте тиімді. Бұл тәсіл ерітінділердің құрамындағы кейбір қиын еритін минералдық және органикалық заттардың катиондар мен аниондардын басқа катиондар мен аниондарға ауыстыру арқылы бөліп алуға негізделген. Судың құрамындағы Са2+, Mg2+ және Fе3+ иондарын бөліп алу үшін катиониттер мен аниониттер қолданылады. Катиониттер ретінде сульфакөмір немесе құрамында Н+, Na+ немесе NH4+ иондарынан тұратын активті топтары бар жоғарымолекулалық шайырлар қолданылады. Аниониттер ретінде құрамында ОН-, HCO3- және С032- иондарынан тұратын активті топтары бар жоғарымолекулалық шайырлар қолданылады. Суды ионалмасу әдісімен жұмсарту үшін құрылысы әртүрлі ионалмасу қондырғылары қолданылады.
Судың құрамы, оны әртүрлі мақсаттарда қолдану мүмкіндігі немесе оны дайындау қажеттілігі техникалық талдау нәтижелерінің негізінде анықталады. Судың толық құрамын анықтау үшін әртүрлі талдау тәсілдері қолданылады және оларды жүргізу үшін өте көп уақыт жұмсалады. Талдау тәсілдері судың температурасын, түсін, иісін, дәмін, қышқылдығын, оттегінің, күкіртті сутектің, көміртек қостотығының, аммоний сульфатының, нитраттардың, нитридтердің, фторидтердің, органикалық заттардың, бикарбонаттардың және т.б. құрамын анықтауға мүмкіндік береді. Бірақ көп жағдайда толық талдау жасаудың кажеті жоқ. Сондықтан тек қана қажетті талдау әдістерін қолданумен шектеледі, оларға судың кермектілігін, тотығуын және сілтілігін анықтау жатады.
3 Жұмысты орындау әдістемесі
3.1 Қондырғылар, техникалық және аспаптық құралдар:
1. Беті жабық электр плиткасы
2. Химиялық ыдыстар
3. Титрлеу қондырғысы
4. Liston A 1210 аквадистилляторы
3.2 Судың карбонатты кермектілігін анықтау
1. Өлшегіш цилиндрдің көмегімен зерттелетін судың 100мл-н (су ағатын құбырдан немесе басқа су көзінен) өлшеп алып, оны конустық қолбаға құяды.
2. Суға 2-3тамшы метилкызғылт индикаторын қосып, тұз қышқылының 0,1н ерітіндісімен (V1) ашық кызғылт түске енгенше титрлейді.
Титрлеу барысында тұз қышқылының кальций бикарбонаттарымен әрекеттесуі кезінде келесі реакция жүреді:
Ca(HCO3)2 + 2HCl = CaCl2 + 2H2O + 2CO2 ↑ |
(5.10) |
3. Судың карбонатты кермектілігін Нк (мг-экв) мына формула бойынша есептейді:
|
(5.11) |
мұндағы: V1 – титрлеуге кеткен 0,1н тұз қышқылының көлемі, мл; 0,0028 – тұз қышқылының кальций оксиді бойынша титрі; 10000 – қайта есептеу коэффиценті; 20,04 – алынған мәліметтерді мг-экв кермектілікке қайта есептеу коэффиценті. |
3.3 Судың жалпы және карбонатты емес кермектілігін анықтау
1. Карбонатты кермектілікті анықтап болғаннан кейін, зерттелетін суды 5-10минут аралығында көмірдің қостотығы кеткенше қайнатады.
2. Тамызғыштың көмегімен 25мл араласпа қоспа (Na2CO3+NaOH) қосып, тағы да 5-10минут аралағында кальций мен магний тұздары тұнбаға түскенше қайнатады, сол кезде келесі реакциялар жүреді:
CaCl2 + Na2CO3= CaCO3 + 2NaCl |
(5.12) |
MgCl2 + 2NaOH = Mg(OH)2 + 2NaCl |
(5.13) |
Mg SO4 + 2NaOH = Mg(OH)2 + Na2SO4 |
(5.14) |
|
|
3. Содан кейін ерітіндіні салқындатып, тұнбасымен бірге көлемі 250мл өлшегіш колбаға ауыстырып, белгіленген белгіге дейін дистилденген сумен сұйылтады.
4. Тұнбаны сүзіп алады. Фильтраттың 100мл көлемін конустық колбаға тамызғыштың көмегімен құяды.
5. Сынамаға 2-3тамшы метилқызғылт индикаторын қосып, тұз қышқылының 0,1н ерітіндісімен (V2) түсі әлсіз қызғылт түске өзгергенше титрлейді.
6. Басқа конусты колбаға араласпа қоспаның (Na2CO3+NaOH) 25мл көлемін құйып алып, оған 2-3тамшы метилқызғылт индикаторын қосып, тұз қышқылының 0,1н ерітіндісімен (V3) түсі әлсіз қызғылт түске өзгергенше титрлейді.
7. Жалпы кермектілікті (Нж) есептеу үшін мына формула қолданылады:
Hж = (V3 – 2,5V2)х1,4 |
(5.15) |
мұндағы:V3 – араласпа қоспаның (Na2CO3+NaOH) 25мл көлемін титрлеуге кеткен 0,1н тұз қышқылының көлемі, мл; V2 – зерттелетін суды титрлеуге кеткен 0,1н тұз қышқылының көлемі, мл; 2,5 – сұйылту коэффиценті. |
8. Карбонатты емес кермектілікті (Нк.е.) жалпы және карбонатты кермектіліктердің айырмасы бойынша есептейді:
Нк.е. = Нж - НК (5.16) |
3.4 Судың тотығуын анықтау
Судың тотығуын анықтау кезінде алынған мәліметтер судың құрамындағы органикалық қоспаларды тотықтыруға қажетті оттегінің мөлшерін жорамалдауға мүмкіндік береді. Судың тотығуын анықтау үшін:
1. Зерттелетін судың 100мл көлемін өлшегіш цилиндрдің көмегімен конустық колбаға құяды.
2. Судың сынамасына 5мл күкірт қышқылының (1:3) ерітіндісін және калий перманганатының 0,01н ерітіндісінің (А) 10мл-н қосады.
3. Ерітіндіні 10минут аралығында қайнатады. Қайнау аяқталғаннан соң ыстық ерітіндіге қымыздық қышқылының 0,01н ерітіндісінің (С) 10мл-н қосып, оның артығын калий перманганатының 0,01н ерітіндісімен (В) әлсіз қызғылт түске енгенше титрлейді.
4. Судың тотығуын X (1л судағы оттегінің мөлшері, мг/л) есептеу үшін мына формула қолданылады:
X=((A+B)-C)х0,08х10 |
(5.17) |
мұндағы: А - органикалық қоспаларды тотықтыру үшін суға құйылған KMnO4–ң 0,01н ерітіндісінің көлемі, мл; В – титрлеуге кеткен KMnO4–ң 0,01н ерітіндісінің көлемі, мл; С - қымыздық қышқылының (Н2С2О4) 0,01н ерітіндісінің көлемі, мл; 0,08 - KMnO4 –ң 0,01н ерітіндісінің 1мл көлеміне сәйкес келетін оттегінің мөлшері, мл; 10 – алынған мәліметтерді мг/л бірлігіне есептеу коэффиценті. |
№6 ЗЕРТХАНАЛЫҚ ЖҰМЫС
КҮКІРТ КОЛЧЕДАНЫН КҮЙДІРУ ПРОЦЕСІН
ОҚЫП ЗЕРТТЕУ
1 Жұмыс мақсаты:
1) Күкірт колчеданын күйдіргенде жүретін әртекті процесті тәжірибе жүзінде оқып зерттеу.
2) Температураның, колчеданды майдалау дәрежесінің және процестің ұзақтығының SO2-нің шығымына (күкірттің жану дәрежесіне) әсерін анықтау және процесті бақылау әдістерін игеру.
3) Процестің тиімді технологиялық ережесін анықтау.
-
Теориялық мәліметтер
2.1 Күкірт қышқылы өндірісінің жалпы сипаттамасы
Күкірт қышқылы химия өнеркәсібінің негізгі өнімдерінің бірі болып саналады. Күкірт қышқылы – май тәріздес, түссіз, иіссіз, тұтқырлы, судан ауыр сұйық зат, сумен кез-келген қатынаста араласады. Өзінің ерекше технологиялық қасиеттеріне байланысты халықшаруашылығының көптеген салаларында қолданылады. Өндірілетін күкірт қышқылының басым бөлігі (30-дан 60%-ға дейін) минералды тыңайтқыштар, бояулар (2-ден 16%-ға дейін), химиялық талшықтар (5-тен 15%-ға дейін) өндірістерінде және металлургияда (2-ден 3%-ға дейін) қолданылады. Сонымен қатар ол тоқыма өнеркәсібінде, сульфаттар, хроматтар, қопарғыш заттар, көптеген органикалық қосылыстар мен бояғыштар өндірістерінде, мұнай өнімдерін және минералды майларды тазартуда қолданылады.
Күкірт қышқылын өндіру әдістері екі түрге бөлінеді: нитрозалық және контактілік (түйістіру). Күкірт диоксидін өндіру сатысы екі әдіске ортақ болып табылады. Нитрозалық әдісте оттегінің көзі және катализатор ретінде азот оксидтері қолданылады. Процестің нәтижесінде азот оксидтерінің қосылыстарымен ластанған төмен сапалы күкірт қышқылы (75-77%H2SO4) өндіріледі. Бұл қышқылды тек қана минералды тыңайтқыштар өндірісінде қолдануға болады. Контактілік әдісте күкірт диоксиді қатты катализатордың бетінде күкірт үшоксидіне тотықтырылады.
Күкірт қышқылы өндірісінде шикізат ретінде элементарлы күкірт, күкіртқұрамдас қосылыстар, құрамында күкірт диоксиді бар қалдықты газдар және гипс қолданылады. Күкіртқұрамдас қосылыстардан күкірт немесе күкірт диоксидін (SO2-нi) алуға болады. Мұндай қосылыстар ретінде темірдің, түрлі-түсті металдардың сульфидтері, сутекті күкірт және т.б. күкіртті қосылыстар қолданылады. Әдетте, негізгі шикізат ретінде темір (күкірт) колчеданы қолданылады, оның негізгі компоненті темір бисульфиді болып табылады.
Күкірт қышқылын өндіру процесі бірнеше сатыдан тұрады. Бірінші сатыда күкіртқұрамдас қосылыстарды (мысалы, колчеданды) күйдіру нәтижесінде құрамында SO2 бар күкіртті газ пайда болады. Содан кейін газ екі сатылы тазарту сатысына жіберіледі. Бұл жерде газ катализаторға зиянды әсер ететін қоспалардан тазартылады. Тазартылған газ кептіру мұнарасында құрағатылып, түйістіру сатысына беріледі. Күкірт диоксидінің контактілік тотығу процесі түйістіру аппараттарында жүзеге асырылады. Бұл аппараттарда катализатор 4-5 қабатқа орналыстырылады. Процесс тиімді температуралар сызығы (ТТС) бойынша 440-6000С-де жүргізіледі. Процестің жоғары жылдамдығын және SO2-нiң жоғары тотығу дәрежесін қамтамасыз ету мақсатымен күкіртті газ катализатордың әрбір қабатынан кейін салқындатылып, келесі қабатқа беріледі. Түйістіру нәтижесінде пайда болған SO3 абсорберлерде шоғырланған күкірт қышқылымен сіңіріледі. Табиғи күкірттің құрамында 99,5%-ға дейін элементарлы күкірт болады, сондықтан табиғи күкірттен өндірілген газды тазартудың қажеті жоқ.
2.2 Колчеданды күйдіру процесінің физика-химиялық негіздері
Күкірт колчеданын күйдіру процесі атмосфералық кысымда құрылыстары әртүрлі пештерде жүзеге асырылады. Колчеданды күйдірген кезде бірнеше реакция жүреді. Алдымен, темір бисульфидінің (FeS2) темір сульфиді (FeS) және бу тәрізді күкіртке термиялық ыдырау реакциясы жүреді:
2FeS2→2FeS+S2-Q |
(6.1) |
Күкірттің бөлінуі 5000С-де басталып, температура жоғарылаған сайын күшейе түседі. Күкірт булары жанып SO2 газын түзеді:
S2+2O2→2SO2+Q |
(6.2) |
Табиғи күкірттің жану процесі де осы реакция бойынша жүреді.
Күкірттің жану жылуы бірінші кезеңде FeS2-і эндотермиялық ыдырату реакциясында қолданылады. Температураны 8000С-ге дейін жоғарылатқан кезде темір сульфиді (FeS) келесі реакция бойынша жанады:
4FeS+7O2→2Fe2O3+4SO2+Q |
(6.3) |
Колчеданды күйдіру процесінің жалпы химиялық теңдеуі:
4FeS2+11O2→2Fe2O3+8SO2+Q |
(6.4) |
|
|
Қосымша FeO және Fe3O4 түзілу реакциялары да жүруі мүмкін. Сондықтан процестің нәтижесінде пайда болған қатты зат – қалдықтың құрамында темір оксидтері (FeO, Fe3O4, Fe2O3) және 0,5-2% жанбаған күкірт болады. Күкіртті газдың құрамында қолданылатын пештің құрылысына байланысты 7-13% SO2, 4-11% O2, 0,5%-ға дейін SO3 және азот болады.
Колчеданды күйдіру процесі
әртекті процестерге жатады, оның жалпы жылдамдығы мынадай теңдеумен
анықталады.
|
(6.5) |
мұндағы:
|
Процестің қозғаушы күшін (ΔС) жоғарылату үшін газды фазадағы (ауадағы) оттегінің концентрациясын жоғарылату және реакциялық аймақтан реакция өнімдерін шығару қажет.
Күйдіру нәтижесінде сульфидтің бетінде темір оксидінің қабықшасы пайда болады, сондықтан колчеданның жанбаған бөлігіне оттегінің жетуі қиындайды, яғни жану процесінің жылдамдығы төмендейді. Бұл процестің жылдамдығы газды реагент оттегінің қатты өнімнің (Fe2O3) беті арқылы диффузиясы және газды өнім SO2-нің қатты өнімнің (Fe2O3) бетінен шекаралық газды қабатқа диффузиясымен шектеледі. Яғни, процесс ішкі диффузиялық аймақта жүреді. Демек, процестің жалпы жылдамдығын жоғарылату үшін ішкі диффузиялық аймақта жүретін процестің жылдамдығына әсер ететін параметрлерді жоғарылату қажет.
Температураны шектен тыс жоғарылату (>850°С) колчеданның түйіршіктерінің балқуына, яғни әрекеттесу бетінің азаюына, соның әсерінен процестің жылдамдығының төмендеуіне алып келеді. Әртекті процестің жылдамдығына жүйені қарқынды араластыру (турбуленттеу) елеулі әсер етеді. Әрекеттесу бетін жоғарылату үшін колчеданды майдалау және араластыру дәрежесін жоғарылату керек. Бірақ майдалау дәрежесін шектен тыс жоғарылату бөлшектердің бірігуіне, яғни әрекеттесу бетінің азаюына алып келеді. Араластыру дәрежесін жоғарылату колчеданның бетінің жаңаруына, колчеданның әрекеттеспеген түйіршіктерінің оттегімен әрекеттесуінің жеңілдеуіне алып келеді.
Колчеданды күйдіру үшін құрылысы әртүрлі пештер қолданылады: механикалық сөрелі пештер, шаңдатып жандыру пештері және «қайнау қабатты» пештері. «Қайнау қабатты» пештері өндірісте қолданылатын ең тиімді пештер болып саналады. «Қайнау қабатты» пештерінің артықшылықтары: өнімділігі жоғары, құрылысы қарапайым, әртүрлі кендерді жандыру үшін қолдануға болады, араластыру дәрежесі жоғары және экзотермиялық реакцияның жылуы толық қолданылады. Бұл пештердің негізгі кемшілігі – алынатын газдың құрамында әртүрлі қоспалар болады, яғни өнімдік газды мұқият тазарту қажет.
3 Қондырғының сипаттамасы және жұмысты орындау әдістемесі
3.1 Қондырғылар, техникалық және аспаптық құралдар:
1. SNOL 0,2/1250 зертханалық түтікті электр пеші
2. Химиялық ыдыстар
3. Титрлеу қондырғысы
4. Liston А 1210 аквадистилляторы
5. ВЛТЭ-150 зертханалық таразысы
6. Суағынды сорғыш
3.2 Қондырғының сипаттамасы
Колчеданды күйдіруге арналған қондырғының сызба-нұсқасы 6.1-ші суретте көрсетілген. Қондырғы кварц түтігі (2) бар түтікті электр пешінен (1) тұрады. Кварц түтіктің ішіне колчедан салынған қайықша (3) орналастырылады. Пештің ішіндегі температураны бақылау және реттеу үшін пеш автоматты бақылау жүйесімен жабдықталған. Реакция аймағындағы температура пештің төменгі жағындағы дисплейде (4) көрсетіледі. Кварц түтіктің бір жағы ашық, ал екінші жағы шыны түтікшеге (7) жалғанған резеңке тығынмен (6) бекітілген. Шыны түтікше (7) арқылы процестің нәтижесінде пайда болған газ сіңіру колбасына (8) жіберіледі. Пештен шыққан газды сіңіру колбасына сіңіру үшін суағынды сорғыш (9) қолданылады.
|
1 – электр пеші, 2 – кварц түтік; 3 –қайықша; 4 – температура индикаторы; 5 – тұрақты ток көзі; 6 – резеңке түтік; 7 – шыны түтікшелер, 8 – сіңіру колбасы, 9 – суағынды сорғыш. 6.1 сурет - Колчеданды күйдіруге арналған қондырғының сызба-нұсқасы. |
3.3 Жұмысты орындау тәртібі
1. Сіңіру колбасына алдын-ала 100мл 0,1н йод ерітіндісін құяды.
2. Жұмысты орындау алдында қондырғының дұрыс жиналғанын тексереді. Пештің түтігін шыны түтікшеге жалғанған резеңке тығынмен мықтап бекітеді.
3. Содан кейін пешті ток көзіне қосады.
4. Колчеданның 0,4грамын аналитикалық таразыда 0,001г дәлдікпен өлшеп алып, қайықшаға салады.
5. Пештегі температура 5000С-ге жеткенде қайықшаны қысқыштың көмегімен кварц түтіктің ішіне салып суағынды сорғышты қосады. Күйдіру процесін 60 минут аралығында жүргізеді.
6. Пештен шығатын газ сіңіру колбасында 0,1н йод ерітіндісімен сіңіріледі. Егер процестің барысында йод ерітіндісі толық түссізденіп кетсе, онда шыны ыдысқа қосымша 25мл 0,1н йод ерітіндісін құю керек.
Сіңіру нәтижесінде йод күкірт диоксидімен әрекеттеседі:
SO2+2H2O+J2=H2SO4+2HJ |
(6.6) |
|
|
7. Процесс уақыты аяқталғаннан кейін пешті ток көзінен ажыратып, қысқыштың көмегімен қайықшаны кварц түтіктің ішінен алады.
9. Шыны ыдыстың ішіндегі ерітіндіге индикатор ретінде крахмал қосып, натрий тиосульфатының 0,1н ерітіндісімен ерітінді түссізденгенше титрлейді. Титрлеу барысында келесі реакция жүреді:
J2+2 Na2S2O3 = 2 NaJ+Na2S4O6 |
(6.7) |
|
|
9. Титрлеуге кеткен ерітіндінің көлемі бойынша жанып кеткен күкірттің салмағын есептейді.
4 Процестің технологиялық көрсеткіштерін есептеу
1. Колчеданның құрамындағы күкірттің мөлшерін біле отырып күкірт толық жанғанда бөлінетін SO2-ң теориялық мөлшерін (Gтеор) есептеуге болады:
Gтеор= |
(6.7) |
мұндағы: а - колчеданның салмағы, г; b - колчедандағы күкірттің құрамы, %; 32 және 64 – сәйкесінше S және SO2–ң молекулалық салмақтары. |
Есептеуді (6.4) реакциясының теңдеуі бойынша жүргізеді.
2. Тәжірибе жүзінде жанып кеткен күкірттің салмағын qS (г) есептеу үшін келесі формула қолданылады:
|
(6.9) |
|
|
мұндағы: 0,0016 - йодтың
күкірт бойынша титрі, 0,1н йод ерітіндісінің 1мл сәйкес күкірттің
мөлшері;
|
3. Алынған күкіртті газдың мөлшері Gтәж (г) :
Gтәж
= |
(6.10) |
4. Күкірттің жану дәрежесі α (%):
|
(6.11) |
5. Күкіртті газдың шыны ыдыс
арқылы өткен уақытын белгілеп =f(
)
кинетикалық қисығын салуға қажет мәліметтерді
алады. Оқытушының тапсырмасы
бойынша күкірттің жану дәрежесінің
температураға немесе колчеданның майдалану дәрежесіне тәуелділігін
зерттеуге болады. Алынған мәліметтерді
6.1-ші кестеге енгізеді. Тағайындалған мәліметтер бойынша
күкіртқұрамдас шикізаттарды күйдіру процесінің тиімді ережесін
анықтауға болады.
6.1 кесте - Колчеданды күйдіру процесінің көрсеткіштері
Тәжірибе№ |
Колчедан ның салма ғы а, г |
Колче- дандағы күкірт-тің құрамы b, % |
Күйді ру темпе-ратура- сы, 0С |
Күй-діру уақы- ты |
Nа2S2O3 ерітінді-сінің
мөлшері |
Жан-ған күкірт-тің мөлше-рі qS, г |
SO2-ң тәжі-рибе-лік мөлше-рі Gтәж, г |
SO2-ң теория лық мөлше-рі Gтеор, г |
Күкірт-тің жану дәреже- сі α, % |
|
|
|
|
|
|
|
|
|
|
5 Қауіпсіздік техникасы
-
Қондырғының дұрыс жиналғанын тексеру керек.
-
Күкіртті ангидрид химиялық улы зат болып табылады. Сондықтан уланған жағдайда жәбірленушіні кауіпті аймақтан алып кетіп, таза ауаға шығару керек. Егер жәбірленуші ес-түссіз болса, онда оған дәрігер келгенше жасанды дем беру керек.
-
Ыстық қайықшаны тек кысқыштың көмегімен алу керек.
-
Қондырғының қорабын, сымдарды қолмен немесе металл заттармен ұстауға рұқсат етілмейді.
-
Күйіп қалған жағдай күйген жерді калий перманганаты немесе ас содасының 2%-ды ерітіндісімен жуу немесе май жағу керек.
6 Бақылау сұрақтары
1. Күкірт қышқылын өндіру тәсілдері.
2. Күкірт қышқылын алу үшін қолданылатын шикізаттар және оларды салыстыру.
3. Күкірт қышқылын өндіру процесінің негізгі сатылары.
4. Күйдіру процесінің жылдамдығы мен күкірттің жану дәрежесі қалай анықталады?
5. Колчеданды күйдіру процесінің жылдамдығына әсер ететін факторлар.
6. Күйдіру процесінің тиімді температурасын негіздеу. Колчеданды күйдіру процесін қарқындату тәсілдері.
7. Темір бисульфидінің тотығу процесінің химизмі.
8. Колчеданды күйдіруге арналған пештер. «Қайнау қабатты» пештерінің артықшылықтары мен кемшіліктері.
№7 ЗЕРТХАНАЛЫҚ ЖҰМЫС
ФЕНОЛ МЕН ФОРМАЛЬДЕГИДТІҢ ПОЛИКОНДЕНСАЦИЯСЫ
-
Жұмыс мақсаты::
-
Фенол мен формальдегидті поликонденсациялау арқылы новолачкалы немесе резолды шайырларды (оқытушының тапсырмасы бойынша) алудың зертханалық және виртуалдық әдістерімен танысу.
-
Зертханалық жұмысты виртуалды ережеде компьютерлік бағдарлама бойынша орындау дағдыларын игеру.
2 Теориялық мәліметтер
Целлюлоза, пластмассалар, каучуктер, резеңкелер, желімдер, қабықшалар және т.б. табиғи және жасанды жоғары молекулалық органикалық қосылыстар (ЖМҚ) халық шаруашылығында кеңінен қолданылады. ЖМҚ негізінде алынған материалдардың қасиеттері алуан түрлі болуы мүмкін, атап айтқанда олар қатты және жұмсақ, жарық өткізетін және өткізбейтін, тығыздығы төмен бола түрып беріктігі жоғары, дыбыс өткізбейтін және химиялық тұрақты болуы мүмкін.
ЖМҚ-полимерлер органикалық қосылыстардың ерекше тобы болып саналады. Олар мономер молекулаларының химиялық әрекеттесуі нәтижесінде пайда болған үлкен молекулалардан (макромолекулалардан) тұрады. Мұндай қосылыстардың құрамына ондаған және мыңдаған атомдар кіреді, ал молекулалық салмақтары бірнеше жүзден ондаған миллион көміртек бірліктерін құрайды.
Алу әдістеріне байланысты ЖМҚ полимеризациялық және поликонденсациялық деп екіге бөлінеді. Екі жағдайда да бастапқы заттың молекуласында бір-бірімен немесе басқа молекулалармен полимерлер түзіп әрекеттестін көмірсутекті байланыстар немесе тұрақсыз циклдік топшалар немесе =С=, С≡С-, =С=О, СН2=СНХ функционалды топшалары, х-галоид, окси-, амино-, циантобы және т.с.с. болуы керек.
Полимеризация дегеніміз мономер молекулаларының үлкен полимер молекуласына бірігу процесі. Полимердің құрамы бастапқы мономерлердің құрамына тең, яғни құрамы өзгермеііді.
|
(7.1) |
мұндағы: R-орынбасар. |
Реакция нәтижесінде төмен молекулалы жанама өнімдер бөлінбейді, реакция қайтымсыз және жылу бөліп жүреді. Полимеризациялық ЖМҚ- ға полиэтилен, поливинилхлорид, полистирол, фторопласт және т.б. жатады
Сополимеризация дегеніміз химиялық құрамы әртүрлі екі немесе бірнеше мономерлердің біріккен полимеризациясы.
Сополимеризация процесі көптеген жағдайда полимеризацияға ұқсас, бірақ келесідей ерекшеліктері бар:
1) сополимеризация процесі құрылысы ұқсас мономерлер арасында жақсы жүреді;
2) бір қатар мономерлер полимерлер түзе алмайды, бірақ құрамы басқа мономерлермен жеңіл сополимеризацияланады.
Поликонденсация дегеніміз мономерлердің бір-бірімен әрекеттесуі нәтижесінде ЖМҚ түзу процесі. Реакция нәтижесінде полимермен қатар төмен молекулалы жанама өнімдер (су, аммиак, көмірқышқыл газы, спирт және т.б.) пайда болады. Бұл поликонденсация процесінің қайтымды екенін көрсетеді. Бастапқы мономерлердің құрамына және реакцияны жүргізу тәсіліне байланысты реакция қайтымды да, қайтымсыз да болуы мүмкін. Қайтымсыз поликонденсация жоғары жылдамдықпен жүреді, ал қайтымды поликоңденсация баяу жүреді. Поликонденсация процесінде көп мөлшерде жылу бөлінетіндіктен (яғни экзотермиялық процесс), тепе-теңдік жағдайда төмен температурада соңғы өнімнің молекулалық салмағы жоғары болады. Сондықтан, процестің жылдамдығын жоғарылату үшін ең алдымен поликонденсацияны жоғары температурада жүргізеді, ал тепе-теңдікке жақындаган сайын температураны төмендетеді.
Фенол-формальдегидті шайырлар поликонденсациялық шайырларға жатады. Фенол-формальдегидті шайырларды алу процесінің тепе-теңдік тұрақтысы Кт=10000 болады. Яғни, процестің тепе-теңдігі дайын өнімнің бағытына қарай ығысады, демек жанама өнім ретінде бөлінетін су поликонденсация процесінің кинетикасына әсер етпейді.
Поликонденсация процесінің жылдамдығы мен бағыты, сонымен қатар алынатын қосылыстардың құрамы мен қасиеттері әрекеттесуші заттардың қатынасы мен қасиеттеріне, функционал топтарының санына, әсерлесетін заттардың әрекетесу бетіне (араластыруға), температураға, түзілген төмен молекулалы жанама өнімдерді реакция аймағынан шығару жиілігіне (тепе-теңдікті жылжыту үшін) және катализатордың қасиеттеріне байланысты болады. Катализатордың мөлшері мен қасиеттеріне және бастапқы реагенттердің қатынасына байланысты термопластикалық (термобалқығыш) және термореактивтік (термоқатты) шайырлар алынады.
Термопластикалық шайырлардың құрылысы сызықты болады, олар қыздырғанда балқиды, ал салқындатқанда қатады және де белгілі бір еріткіштерде ериді.
Термореактивті шайырлардың құрылысы торлы жазық немесе кеңістікті болады, сонымен қатар оларды қыздырғанда немесе ұзақ уақыт сақтағанда олар балқымайды және ерімейді.
Термопластикалық шайырларды кейде наволочкалы шайырлар деп те атайды. 7моль фенолға 6моль формальдегид қосып, катализатор ретінде минералды қышқылдарды (HC1, H3PO4, H2SO4) пайдаланғанда наволочкалы шайыр түзіледі:
nCH2O+(n+1)C6H5OH→H-(C6H3(OH)CH2)n-C5H4OH+H2O |
(7.2) |
Құрылысы сызықты шайырдың құрылымдық формуласы:
мұндағы: n – полимеризация дәрежесі, ол жоғарымолекулалық қосылыстың ұзындығын анықтайтын қайталанатын элементарлы бөліктердің санын сипаттайды (n=4+8).
Фенол мен формальдегидтің молярлық қатынасы неғұрлым аз болса, соғүрлым алынатын шайырдың молекулалық салмағы көп болады. Поликонденсация уақыты ұзақ болса фенол мен формальдегид толық байланысады және дайын өнімнің орташа молекулалык салмағы жоғарылайды. Наволочкалы шайырлар пресс-ұнтақ, абразивті және т.б. материалдар алу үшін қолданылады.
Бастапқы қоспада формальдегидтің мөлшері артық болғанда (6моль фенолға 7 және одан да көп моль формальдегид қосқанда) және катализатор ретінде сілтілерді (NH4OH, NaOH, Ва(ОН)2) немесе сілтілік металдардың тұздарын пайдаланғанда термореактивтік немесе резолды шайырларды алуға болады. Резолды шайырлар 1200С-ден жоғары қыздарғанда балқымайтын, ерімейтін күйге өтеді.
Қату дәрежесіне байланысты резолды шайырлар үш күйге бөлінеді:
а) резол (бакелит А) – жоғары молекулалық өнімдердің қоспасы, қыздырғанда және спиртпен немесе ацетонмен әрекеттескенде ериді, сызықты құрылымға ие. Бұл саты 70-75°С-де жүреді.
ә) резолды 90°С-ге дейін қыздырғанда немесе ұзақ уақыт сақтағанда ол резитолға (бакелит В) айналады. Резитол тармақталған құрылымға ие, жартылай спиртте немесе ацетонда ериді, соның әсерінен ісінеді. Қыздырғанда балқымайды, жұмсарып созылмалы күйге өтеді.
б) резит (бакелит С) - поликонденсацияның соңғы сатысы, дайын өнімді өндірген кезде жүреді. Қыздырған кезде резит жұмсармайды және еріткіштерде ісінбейді.
Резолдың резитолға айналуына байланысты резолды шайырларды өндіру наволочкалы шайырларды өндіруге қарағанда әлде қайда күрделі болып саналады.
3 Қондырғының сипаттамасы және жұмысты орындау әдістемесі
3.1 Қондырғылар, техникалық және аспаптық құралдар:
1. Шайырды синтездеу қондырғысы
2. Химиялық ыдыстар
3. ВЛТЭ-150 зертханалық таразысы
4. Беті жабық электр плиткасы
5. Құм моншасы
6. Су моншасы
3.2 Қондырғының сипаттамасы
Шайыр алуға арналған қондырғының сызба-нұсқасы 8-ші суретте көрсетілген. Ол су моншасына (2) орналастырылған және штативке бекітілген үш мойынды колбадан (1) тұрады. Колбаның ортаңғы мойнына ішкі қуысында араластырғышы (3) бар кері мұздатқыш (5) қосылған. Араластырғыш (3) электр қозғалтқыштың (4) көмегімен іске қосылады. Температура термометрдің (6) көмегімен реттеледі. Су моншасын қыздыру үшін беті жабық электр плиткасы (8) қолданылады.
.
3.3 Наволочкалы шайырды алу процесін жүргізу тәртібі
1. (1,12-1,42):1 молярлық қатынаста алынған фенол мен формальдегидтің (формалиннің) қоспасын бөлме температурасында колбаға салып, толық ерігенше араластырады. Реагенттердің шығынын 10-20г. фенолға есептейді.
2. Фенол толық ерігеннен кейін колбаға HC1 немесе H2SO4 катализаторын (фенолдың салмағынан 0,3-тен 1-1,5%-ға дейін) қосады. Содан кейін колбаны кері мұздатқышқа жалғап, алдын-ала 90-1000С-ге дейін қыздырылған су моншасына орналастырады. Процесс барысында қоспаны араластырғыштың көмегімен үздіксіз араластырады.
3. Реакцияны су қабатының көлемі тұрақты болғанға дейін жүргізеді. Реакцияның аяқталуын байқау үшін колбаның бүйір мойнынан қоспаны алып, оны салқындатады. Реакцияның соңын тұрақты лай пайда болғанынан көреді. Ол үшін 3-5мл қоспаны алып, фарфор ыдысқа құяды. Кейін ыдысты қыздырып, қоспаның құрамындағы суды буландырып, шайыр қата ма қатпай ма, соны бақылайды. Егер шайыр қатпаса қайнатуды жалғастыра береді.
4. Фенолдың формальдегидпен әрекеттесу реакциясының жүру қарқындылығын бақылау керек. Қалыпты жағдайда қоспаны 90-950С-ге дейін қыздырады. Егер қоспа қатты кайнап кетсе (қыздырғаннан 20-40 минуттан кейін), онда қыздыруды тез арада тоқтатып, моншадан колбаны алып қояды. Біршама уақыт аралығында реакция қыздырусыз жүреді (температура 1000С-ден жоғарылағанда процесс конденсация реакциясының жылуының әсерінен жүреді).
5. Реакция тоқтағаннан кейін колбаны қайтадан қайнап түрған су моншасына орналастырып, қоспа тұрақты екі қабатқа бөлінгенше реакцияны жалғастырады. Фенолдың формальдегидпен әрекеттесу реакциясы аяқталған соң, қыздыруды тез арада тоқтатып, су қабатын тұндырады.
6. Қоспаның бетіндегі суды төгіп тастап, шайырды жылдам фарфор ыдысқа (алдын-ала салмағы өлшенген) құйып алдымен су моншасында, содан кейін құм моншасында кептіреді. Кептіру кезінде шайырды шыны таяқшаның көмегімен үздіксіз араластырып отырып 130-160°С-де жүргізу қажет. Таяқшаға қатып калған тамшылар оңай майдаланатын болған жағдайда кептіруді тоқтатады. Содан кейін алынған шайырдың салмағын өлшейді және шайырдың шығымын есептейді.
|
1 - үшмойынды колба; 2 – су моншасы; 3 - араластырғыш; 4 - қозғалтқыш; 5 - кері мұздатқыш; 6 - термометр; 7 – тығын; 8 – электр плиткасы. 7.1 сурет - Зертханалық қондырғының сызба-нұсқасы. |
3.4 Резолды шайырды алу процесін жүргізу тәртібі
1. Фенолдан, 37%-ды формалиннен және 25%-ды аммоний гидроксидінің ерітіндісінен тұратын қоспаны (1моль фенолға 1,16моль формалин және фенол салмағынан 1,5% NH3) дөңгелек табанды колбаға құйып, толық ерігенше араластырады.
2. Колбаны кері мұздатқышпен байланыстырып (араластырғыш косулы болуы керек), 90-95°С-ге (қоспаның қайнау температурасы) дейін қыздырады.
3. Конденсация реакциясын аяқтау мақсатымен қоспаны 10-15минут аралығында қыздырады. Реакцияның аяқталғанын білу үшін реакциялық қоспанының 2-Змл-н пипетканың көмегімен пробиркаға құйып алады. Пробирканы сілкіп қоспаның температурасын 10°С-ге төмендетіп, лайлануын байқайды.
4. Күшті лайлану реакцияның аяқталғанын көрсетеді. Егер лай пайда болмаса, қыздыруды тағы да 10-15минут жалғастырып, тағы да лайлығын тексереді. Осылай әр 10-15минут сайын қайталайды.
5. Процесс аяқталғаннан соң қыздыруды тоқтатып, қыздырғыш пен араластырғышты өшіріп, мұздатқышты ажыратып, колбаның ішіндегі қоспаны фарфор ыдысқа (алдын-ала салмағы өлшенген) құйып алады. Шайырды салқындатып, оның бетіндегі суды төгіп тастайды. Кейін қалған шайырды бірнеше қайтара сумен жуып, салмағын өлшейді.
6. Алынған шайырдың салмағын таразыда өлшейді. Шайырдың түсі ашық сарыдан қоңыр түске дейін болады. Температураның шектен тыс жоғарылату шайырдың қатты балқымайтыи күйге (резитке) айналуына алып келуі мүмкін.
3.4 Виртуалдық жұмысты орындау әдістемесі
Виртуалды жұмысты орындау үшін студент ең алдымен келесі тесттік сұрақтарға жауап беруі керек:
1. Наволочкалы шайыр алу үшін қолданылатын бастапқы реагенттер.
2. Резолды шайыр алу үшін қолданылатын бастапқы реагенттер.
3. Наволочкалы шайыр алудағы фенол мен формальдегидтің молярлық қатынасы.
4. Резолды шайыр алудағы фенол мен формальдегидтің молярлық қатынасы.
5. Фенол-формальдегид шайырын алу температурасы.
6. Шайыр алу процесіндегі катализатордың шығыны, % фенолдың салмағынан.
7. Резол шайырының катализаторы.
8. Наволочкалы шайыр қай топқа жатады?
9. Наволочкалы шайыр алу процесінің соңын анықтау тәсілі.
10. Фенол-формальдегид шайырын алу процесінде қандай реакциялар жүреді?
11. Реакциялық қоспаны қыздыру үшін қолданылатын аспап.
Ұсынылған 11 сұрақтың 11-не дұрыс жауап бергеннен кейін студент жұмысты орындауға рұқсат алады. Ең болмағанда бір сұраққа дұрыс емес жауап берген жағдайда студент қайтадан бағдарламаның басына көшіп, тест-рұқсатты қайта тапсыруы керек.
Содан кейін студент негізгі реакцияның теңдеуі бойынша 10грамм фенолға жұмсалатын формальдегидтің мольдік және салмақтық шығынын есептеп, сәйкесті ұяшыққа енгізеді. Содан кейін катализатордың түрін таңдап, оның шығынын есептеп, мәнін сәйкесті ұяшыққа енгізеді. Мәліметтер дұрыс емес енгізілген жағдайда «қосу» батырмасын басқан кезде жіберілген қателер көрсетіледі, оларды дұрыстау керек. Барлық мәліметтер дұрыс енгізілген жағдайда жұмысты орындауға көшуге болады. Виртуалды жағдайларды нақты жағдайларға жақындату мақсатында компьютерде температураның уақытқа тәуелділігі көрсетіледі. Температура 1000С болғанда «өшіру» батырмасын басады. Температура 800С-ге дейін төмендегеннен кейін қайтадан «қосу» батырмасын басады. Жұмыс аяқталғаннан кейін компьютерде «дайын» батырмасы іске қосылады. Оны басқанда компьютердің сәйкесті ұяшығында алынған шайырдың салмағы мен құрылымдық формуласы көрсетіледі. Мәліметтерді жазып алу керек.
Студенттің процестің теориялық негіздерін игеру дәрежесін бағалау үшін оған жұмысты қорғауға арналған 20 сұрақтан тұратын тесттік тапсырмалар ұсынылады:
1. Құрылымы сызықтық шайыр…
2. Термопластикалық шайырлардың құрылымы қандай?
3. Қай шайыр термореактивтігі жатпайды?
4. Бакелит В – бұл…
5. Фенол-формальдегид шайырын алу реакциясы…
6. Наволочкалы шайыр алу реакциясы…
7. Полимеризациялық шайыр – бұл…
8. Поликонденсациялық шайырлардың полимеразиялықтармен салыстырғандағы кемшіліктері…
9. Фенол-формальдегид шайырын алу процесі – бұл…
10. Поликонденсация процесін жүргізуге арналған реактор
11. Резиттің басқа резолды шайырлардан ерекшелігі
12. Поликонденсация нәтижесінде пайда болатын төменмолекулалық өнім
13. Резол шайырының катализаторы
14. Шайыр синтезінің тепе-теңдік тұрақтысы нені көрсетеді?
15. Фенол-формальдегидті шайырды поликонденсациялаудың температуралық ережесі
16. Температуралық ережені таңдаудың негіздеу?
17. Поликонденсация процесінің жылдамдығына әсер етпейтін фактор
18. n(CH2 = CHR) (– CH2 – CHR –)n реакциясы – бұл…
19. Сополимеризация – бұл ...
20. Поликонденсация – бұл ... .
Тесттік тапсырманы табысты тапсырғаннан кейін студентке баға қойылады. Егер жұмысты орындау барысында студент 3-тен көп қате жіберсе, онда ол жұмысты қайта орындауы керек.
Бағдарламаның ұяшықтарының сипаттамасы және олармен жұмыс орындау тәсілі
|
1 – Зертханалық жұмыстың теориялық негіздерін көрсететін батырма. 2 - Тест-рұқсат батырмасы. 3 - Бағдарламамен жұмыс орындау туралы қысқаша мәліметтер батырмасы. 7.2 сурет - Бағдарламаның бастапқы терезесі. |
|
7.3 сурет. Тест-рұқсат терезесі |
1) Дұрыс жауапты таңдау үшін бағыттағышты дұрыс жауапқа алып келіп сол жақтағы батырманы басады.
2) Келесі сұраққа көшу үшін «принять» деген батырманы басады.
|
10-анықтамалар алу батырмасы 7.4 сурет - Бағдарламаның интерфейсі. |
Таймер қыздырғышты іске қосқаннан кейін қосылып, процестің жұмыс уақытын көрсетеді. «Температура» деген ұяшықта колбадағы температура көрсетіледі.
|
1 – алынған шайырдың салмағын көрсететін ұяшық. 2 – алынған судың салмағын көрсететін ұяшық. 3 – алынған шайырдың құрылыстық формуласын көрсететін ұяшық. 4 – тест-қорғау батырмасы. 7.5 сурет - Жұмыстың нәтижелерін көрсету терезесі. |
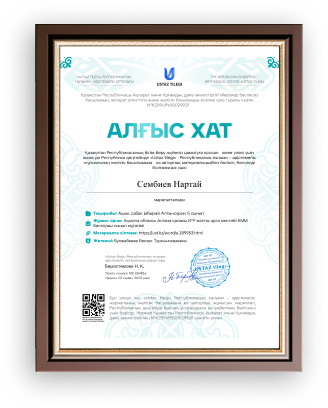
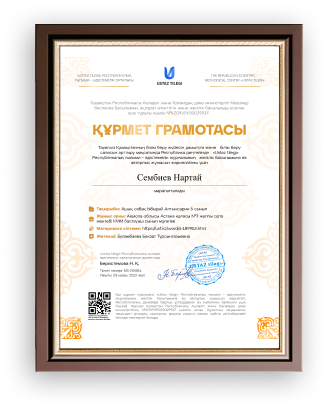