Бұл материал сайт қолданушысы жариялаған. Материалдың ішінде жазылған барлық ақпаратқа жауапкершілікті жариялаған қолданушы жауап береді. Ұстаз тілегі тек ақпаратты таратуға қолдау көрсетеді. Егер материал сіздің авторлық құқығыңызды бұзған болса немесе басқа да себептермен сайттан өшіру керек деп ойласаңыз осында жазыңыз
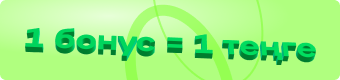
Бонусты жинап картаңызға (kaspi Gold, Halyk bank) шығарып аласыз
Lathe book.

COMPLETELY UPDATED AND REVISED
THE
ERNIE CONOVER
BOOK
A Complete Guide
to the Machine and
Its Accessories


The Lathe
Book
A Complete Guide to the Machine
and Its Accessories
Completely Revised and Updated
Ernie Conover
The Taunton Press

Publisher: JIM CHILDS
Editor: HELEN ALBERT
Associate Editor: JENNIFER RENJILIAN
Copy Editor: DIANE SINITSKY
Indexer: LYNDA STANNARD
Cover Designer: LYNNE PHILLIPS
Interior Designer: MARY McKEON
Layout Artist: ROSALIE VACCARO
Front Cover Photographer: SCOTT PHILLIPS
Back Cover Photographer (author photo ): RANDY O'ROURKE
Interior Photographer: ERNIE CONOVER, except where noted
Illustrator: MARIO FERRO
Text © 2001 by Ernie Conover
Photographs by Ernie Conover © 2001 by The Taunton Press, Inc.
Illustrations © 2001 by Mario Ferro
All rights reserved.
Printed in the United States of America
10 9 8 7 6 5
The Taunton Press, Inc., 63 South Main Street, PO Box 5506,
Newtown, CT 06470-5506
e-mail: tp@taunton.com
Library of Congress Cataloging-in-Publication Data
Conover, Ernie.
The lathe book: a complete guide to the machine and its accessories /
Ernie Conover.-Completely rev. and updated.
p. cm.
Includes index.
ISBN-13: 978-1-56158-416-1
ISBN-10: 1-56158-416-9
1. Lathes. 2. Turning. 1. Title.
TT201 .C66 2001
684' .083---dc21 00-066300

To my mother and father. Both talented artists, tl1ey have always
nurtured a quest for knowledge and lave of art, craft, and history.
Acknowledgtnents
Writing a book is a big undertaking, and I would like to thank the following people who were extremely generous with their time and
were long-suffering in reviewing material and discussing their opinions:
Clead Christiansen; Tim Clay of Oneway Manufacturing; Barrey Frey of
Safetronics Inc.; Peter Gill of Robert Sorby Ltd.; Jerry Glaser of Glaser
Engineering Company; Dave Hout; Kevin Kee of Delta International
Machinery Corp.; Brian Latimer of Teknatool International Ltd.; Darrel
Nish of Craft Supplies USA; and Brad Packard of Packard Woodworks.
I'd particularly like to thank Teknatool International Ltd. and Woodcraft
Supply Corp. for supplying the Nova 3000 on which many of the photos
in this book were shot.
I would like to give special mention to my good friends at KSK Color
Labs. They ran test clips, pushed, pulled, and normally processed all of the
film for this book in an expeditious manner.
I'd also like to thank all of the folks at The Taunton Press, with
special mention to Helen Albert and my editor Jennifer Renjilian.
ABOUT YOUR SAFETY
Working with wood is inherently dangerous. Using hand or power tools
improperly or ignoring safety practices can lead to permanent injury or
even death. Don't try to perform operations you learn about here {or
elsewhere} unless you're certain they are safe for you. If something about
an operation doesn't feel right, don't do it. Look for another way. We
want you to enjoy the craft, so please keep safety foremost in your mind
whenever you're in the shop.

Contents
Introduction 2
Chapter 1 -The Turning Machine 4
Lathe Construction 5
Lathe Anatomy 11
Chapter 2 -Choosing and Buying a Lathe 27
Entry-Level Lathes 29
Mid-Range Lathes 30
Dream Lathes 31
Specialty Lathes 32
Chapter 3 -Setting Up a Lathe 35
Workflow 35
Machine Placement 35
Chip Removal and Ventilation 37
Electrical Service 37
��� �
Tool Storage 38
Chapter 4 -Holding the Work 39
Centers 40
Faceplates 45
Special-Purpose Chucks 53
Chapter 5 -Accessories 75
Steady Rests 75
Arm Rests 77
Sharpening Equipment 80
Safety Equipment 98
Jigs for Special Techniques 101
Lathe Duplicators 111

Chapter 6 -Tools
Gouges
Chisels
Scrapers
Hook and Ring Tools
Chatter Tools
Chasers
Chapter 7 -Maintenance, Repair,
and Modification
Routine Maintenance
Replacing Bearings
Drive Pulleys, Belts, and Motors
Removing Seized Morse Tapers and Faceplates
Tool Rests
Modifying a Lathe
Restoring a Used Lathe
Chapter 8 -Turning Techniques
Coves and Beads
Turning Square to Round
Faceplate Turning
Sanding
Finishing
Glossary
Resources
Index
112
115
124
137
143
144
145
147
147
149
155
158
160
161
164
165
165
171
172
176
180
181
184
186

Introduction
In this book, I will share with you my love of the woodturning lathe. This is a book with a difference because it doesn't focus on the lathe
to the exclusion of all other woodworking. Rather, it treats the lathe as
another essential tool in the woodworking shop-a tool that can expand
your woodworking horizon and add pizzazz to your work. All woodworkers
need to be more familiar with the lathe because at some point your wood
working projects will require turned parts.
When The Taunton Press asked me to do the second edition of The
Lathe Book, I was delighted, but I never realized that rewriting is much
more difficult than writing. Much has changed since the first edition, so
there are many new machines, accessories, and gadgets to share. Turning
is becoming gentrified, and there are now tools and accessories that had
never before been dreamed of. While the philosophical side of me laments
the simplicity lost, the tool junkie side of me opens each "absolutely indis
pensable" new piece of hardware with childlike enthusiasm. My wife,
Susan, appropriately bought me a T-shirt claiming, "He who dies with
the most tools wins." I am in serious contention for the grand prize.
I am also a better turner today than I was eight years ago and have
taught scores of people to turn, so I can tell the story better. Because I
have also written Turning for Furniture Makers (a detailed spindle-turning
book with an accompanying video) and Turn a Bowl with Ernie Conover
(an action manual for bowl turners) since the first edition of The Lathe
Book, I decided to drop some of the techniques and concentrate more on
the lathe and it accessories. The tool chapter is much more readable and
the illustrations are better. Photography is entirely new and in color.

Turning books generally speak to dedicated turners who pursue turning
to the exclusion of all other forms of woodworking. But most woodworkers
are interested in turning only enough to use the lathe in their general
woodworking. Additionally, most turning books miss the mark because
they never really teach you to turn. They talk about equipment, philoso
phy, and history, but they never truly teach turning. With that in mind,
I've tried to keep this a wood turning book that speaks to all woodworkers
and gives the information necessary to be able to employ turning in furni
ture making. This book also offers much to the pure turner. A second
objective is to offer advice on buying, maintaining, modifying, and repair
ing lathes. A good part of the book is devoted to the intricacies of lathes
and their accessories.
I grew up at the lathe, and I've been turning both wood and metal since
I was 12 years old. I understand lathes and how they work. For many years,
my father and I owned a company that produced a lathe we codesigned
the Conover Lathe. An outgrowth of our lathe-manufacturing business is
Conover Workshops, a woodworking school that my wife and I now run
year-round. In 24 years of running the school, I've taught hundreds of
people to turn and have a fair sense of where the hurdles are in the
learning process.
It's my firm belief that most people have the ability to turn, but this skill
has been buried deep inside during the process of growing up. In many
cases, it has been masked by fear and dull tools. If you read through the
next 180 or so pages, I think you'll be able to regain your instinctive turn
ing skill and have some fun in the process. I look forward to this book
starting a revolution in your workshop.
Introduction 3

chapter
1
The Turning
Machine
W oodturning is the art of shaping a rotating piece of wood by the
application of sharp tools. The machine that holds and rotates
the wood is a lathe. The wood turning lathe is a simple work
shop tool that can greatly expand your woodworking horizon. If you want
to shape table legs, chair spindles, and bedposts or add embellishments to
your furniture in the form of drawer pulls, cabinet knobs, and finials, then
you need a lathe. And if you want to make bowls, plates, stool seats, table
tops, and lidded boxes, a lathe is an indispensable machine.
In spindle turning, the grain of the wood being turned runs between
the centers of the lathe, that is, parallel to the axis of the lathe (see the
illustration on the facing page). You would spindle-turn table legs, porch
columns, and chair rungs. In faceplate turning, however, the grain of the
work runs at right angles to the axis of the lathe. You would faceplate-turn
large drawer pulls and bowls.
Most lathes are supplied with basic chucks-a set of centers and a
faceplate. Some people mistakenly think the type of turning is dictated by
the type of chuck used to hold the work. For example, many woodworkers
associate turning between centers with spindle turning, but it's possible to
hold work between centers and yet be faceplate turning. Similarly, it's pos
sible to spindle-turn while having a piece screwed onto a faceplate. (The
screws in this case would be into the end grain of the wood.) The impor
tant thing to remember is that the orientation of the grain, not how the
work is held, dictates whether you are spindle or faceplate turning. It is
imperative to understand this distinction because each type of work
requires different tools and turning techniques, as you shall see in chap
ter 4. In fact, using spindle tools for faceplate work can be dangerous.

Spindle turning
Grain runs parallel
to rotational axis
of lathe.
Faceplate turning
Grain runs at
right angles to
rotational axis.
Spindle Turning vs. Faceplate Turning
Lathes range in size from gigantic industrial machines for architectural
turning to Lilliputian lathes for turning pens and dollhouse furniture.
Knowing about the construction and anatomy will help you choose the
right lathe and get it to work more effectively. The type of lathe you need
will depend to a large extent on the kind of work (and the amount of turn
ing) you plan to do. For example, if you occasionally want to turn a few
chair legs, a light-duty lathe would be more than adequate, whereas heavy
bowl turning would require a much sturdier and larger machine. However,
there are certain desirable features you should look for in any lathe, so I've
drawn attention to these throughout this section to help you make an
intelligent buying decision (see chapter 2 for more on choosing a lathe).
Lathe Construction
The earliest lathes were made of wood, and the use of wood as a bed mate
rial has survived to the present (I designed and turn on such a lathe). More
commonly today, though, lathes are made with all-metal parts. You're likely
to encounter several lathe-construction materials: cast iron, fabricated
steel, steel stampings, cast aluminum, cast zinc, and extruded aluminum. I
have not mentioned plastic here because it is not yet used in major struc
tural components; rather it is reserved for handles, knobs, and housings.
Lathe Construction 5

THE LATHE IS ONE OF THE OLDEST complex tools known to
man, but determining an exact date of its invention is
impossible. The first lathes were undoubtedly spring
pole or bow lathes that were powered by the opera
tor. On a typical spring-pole lathe, the work was held
between a set of "dead" centers, which were merely
metal pOints (see the drawing on the facing page).
Except for these two metal points, the rest of the lathe
was wood.
The bed of the lathe consisted of two stout timbers.
On this was mounted a set of "poppits," which carried
the dead center points. A rope was attached to a tree
branch above the lathe, wrapped several times around
the work, and attached to a lever arm that the turner
moved up and down with his foot. Cutting was only
accomplished on the down stroke, the tree branch
providing a mild spring to return the rope for another
power stroke.
Later, during medieval times, the pole lathe was
brought inside, and the tree branch was replaced with
a long bow mounted above the lathe. The rather pow
erful bow had two strings that passed through off
center holes in a large wood spool onto which the
rope was wound. Stepping down on the lever arm
turned the work, wound the spool, and compressed
the bow. The bow then turned the spool in the oppo
site direction, revolving the work backward and return
ing the lever arm to the up position.
A later bow lathe replaced the tree branch and rope
with a small bow. The bow was grasped by the opera
tor and seesawed back and forth. Unless a helper
could be found, the operator had to hold the tool with
one hand. In India, Afghanistan, and Southeast Asia, it
is still common to see workers using bow lathes on
the ground and guiding the tools with their toes and
left hands while they work the bows with their right.
These early lathes could only turn between centers
because poppits carried immovable, or dead, centers.
Modern lathes came about when the left-hand poppit
was given a rotating, or live, spindle and the right pop
pit was given a retracting spindle. Thus, the headstock
and tailstock were born. Needless to say, the head
stock also made modern faceplate turning possible.
The first live spindle was nothing more than a steel
spindle that frt precisely bored holes in each end of a
cast-iron frame. These were called plane bearings. In
the 19th century, plane bearings gave way to babbitt,
ball, and roller bearings.
These innovations made possible the construction of
the great-wheel lathe. In this type of lathe, a pulley on
the headstock spindle was belted to a large, or great,
wheel 4 ft. to 10 ft. dia. The great-wheel lathe was a
direct product of the guild system, under which appren
tices or slaves would turn the wheels. Later, water,
steam, and gasoline provided the muscle, allowing the
great wheel to be replaced by an overhead shaft.
Of great concern to turners is the amount of vibration inherent in a
lathe. Any turning convention will find turners waxing lyrical about how
quiet and vibration-free their pet lathes are. Any machine has a natural
frequency of vibration when given an impulse from a variety of sources
such as the motor, work by the operator, or in the case of lathes the work
itself. The natural frequency of vibration is the frequency at which the
machine will continue to vibrate after an initial impulse, regardless of the
source. This frequency is directly proportional to the stiffness of the build
ing material and inversely proportional to mass. This means that the stiffer
the material, the higher the frequency, but the more massive the machine,
the lower the frequency. The old adage that "you can't beat a good heavy
machine" is undoubtedly true.
6 The Turning Machine
CAST IRON
Cast iron is a time-honored material for lathe construction that's still hard
to beat. The inherent mass of cast iron combined with a favorable modulus
of vibration makes for a sweet-running machine. Most woodworking

Head poppit
Turner places foot in loop
to provide power.
Pole Lathe
Work spins on set
of greased 60°
dead centers.
Wood wedges hold
poppits to bed.
Most machines come with a 12-in. rest, which is fine for most turning situations.
Tail poppit
Lathe Construction 7

8 The Turning Machine
machinery is cast from grade-25 gray iron, which has a nice balance
between strength, damping effect, and machinability. Castings require
expensive tooling in the form of patterns, and the casting process itself
is expensive-especially in small lots.
Top-quality lathes are made with a heavy cast-iron headstock, tail
stock, and tool-rest assembly. In the past, the bed would also have been
cast iron, but today makers are increasingly turning to fabricated structural
steel as the bed material.
A lathe with cast-iron major components mounted on a wooden bed
is known as a "High Wycombe lathe," so named after the lathes that were
popular with turners who turned furniture parts around High Wycombe,
England, until the early part of the 20th century. Many of the photographs
in this book are of a High Wycombe lathe that I codesigned.
The best economy lathes are often made with cast-iron parts, but the
castings are light in keeping with the lathe. On more expensive lathes, the
castings are "filled"-a substance not unlike auto body filler is squeegeed
on the castings-before painting, resulting in a much better paint job.
This difference is purely cosmetic but does reflect the attitude of the
manufacturer, just as a better car has a better finish.
FABRICATED STEEL
Fabricated lathes are made by welding together pieces of structural steel.
Fabrication first became popular in the late 1950s as a less-expensive alter
native to cast-iron castings. Its biggest advantage is that little or no tooling
The Oneway is an excellent example of a high-end lathe that makes extensive use of fabri
cated structural steel in its manufacture.

cost is required, which makes fabrication particularly well suited to small
production runs where amortizing the costs of patterns for castings would
be difficult. While traditional machine-design theory holds that steel has
poor damping qualities compared with grade-2S cast iron, that's only part
of the story. It is true that the stiffness of steel makes for high-frequency
vibration, but the welds tend to act as barriers to the transmission of vibra
tion. Instead they act much like a cracked glass, stopping vibration.
Fabrication is used in both the most expensive and the cheapest lathes,
so use common sense when making buying decisions.
STEEL STAMPINGS
Steel stampings are made by placing sheet steel between male and female
dies mounted in a press. The press closes the dies on the sheet steel and
forms it into the desired shape. Complicated shapes often entail a progres
sion of dies. The cost of the dies for stamping parts can be considerable,
but the stamping process itself (unlike foundry work) is cheap. This makes
traditional stampings great for high-production work but expensive for
short-run work. The last decade has seen the introduction of computer
numeric machines that can do short-run stamping on a cost-effective basis.
These machines can "nibble" out the basic shape with small round or
square dies, then form the material on various standard-forming dies. A
stamping made from heavy-gauge metal can be very good, but the most
charitable thing that can be said about stampings from light-gauge mate
rial is that they are vibration prone. Stampings are used extensively for
machine stands, belt covers, and the like.
CAST ALUMINUM AND ZINC
Parts such as pulleys, knobs, and hand wheels are often made from cast alu
minum or zinc. These are often called die castings because the low melting
temperature of aluminum and zinc allows them to be cast in metal molds
or dies. Die castings are almost perfect directly from the mold and require
little machining. The low weight of aluminum makes it a good material for
pulleys because balancing is less of a problem than with cast-iron pulleys.
Die-cast knobs and levers are a much better option than plastic.
EXTRUDED ALUMINUM
Occasionally lathes are made of extruded aluminum. Although extrusions
can be tempered, the alloys used for the process are soft and gummy. This
softness, as well as the tendency of raw aluminum to turn anything it
touches black, is somewhat lessened by anodizing, a plating process that
puts a thin, hard coat of aluminum oxide on the surface of the metal.
However, dents that go through the anodized surface into the soft alu
minum substrate are a potential problem.
There are more and more extrusions being used in woodworking
machinery today-my table saw fence is an extrusion, for example.
Although extrusions are acceptable for miniature lathes and parts of
Lathe Construction 9

Headstock
Motor mounts
inside stand or at
back of headstock.
On/off
switch
�
Speed
control
lever for
variable
speed
Sheet-metal stand
10 The Turning Machine
Everylathe
Tool rest
Tool rest
Tool base
Tool base
lock lever
Spindle lock
Spindle
Some lathes now
have modular beds
which allow beds
to be lengthened.
Wood-leg stand
Tailstock
Tailstock
handwheel
Cross beam
lathes, I'm not convinced that they are suitable for an entire full-sized
machine. Before you buy a lathe made principally of extrusions, consider
how much and what type of use you intend for the machine.
HYBRID DESIGNS
Most lathes available today are hybrid designs, incorporating two or more
of the construction materials outlined above. A common design is a cast
iron headstock, tailstock, and tool base mounted on a structural-steel bed
or, on economy lathes, on solid-or hollow-steel tubing. Steel stampings,
sheet metal, aluminum extrusions, and plastic are often used for stands,
belt covers, and knobs.

Lathe Anatomy
Lathes come in all makes and sizes, from bench top models to industrial
heavyweights, but the basic design is the same on all lathes. A rigid bed
supports a stationary headstock and a tailstock that can be moved to
accommodate wood blanks of various lengths. A motor turns a spindle
mounted in the headstock, which in turn drives the work. The illustration
on the facing page shows a composite woodturning lathe combining the
features of many lathes. I call this lathe "Everylathe" because there is prob
ably no lathe that would have all of the features shown-at least at an
affordable price. Let's look at the parts in detail.
THE BED
The lathe bed supports the headstock, tailstock, and tool-rest assembly and
is in turn supported by a stand. The earliest lathe beds were no more than
two wood planks, and wood is still used on some modern lathes. Wood has
much to recommend itself as a bed material-it is relatively inexpensive,
readily available, absorbs vibration, and can yield a lathe of any desired
length between centers. The springiness of a timber bed has shock
absorbing characteristics unmatched by metal.
Starting in the 18th century, cast-iron lathe beds began to displace
wood. Cast iron is a good bed material because it is stable and has excel
lent vibration-damping characteristics. The casting process allows beds of
intricate design to be made. In an iron bed, each of the wood planks is
replaced by a strip, or rib, which is called a "way." The bed ways are typi
cally 1 in. to 11� in. apart. A number of lathes today offer modular cast-
A number of lathes offer modular beds so that any reasonable length between centers is
possible. This Nova 3000 has 20-in. sections.
Lathe Anatomy 11

12 The Turning Machine
iron beds (see the photo on p. 11). Under this scheme, the standard pack
age gives the turner a decent distance between centers, but additional sec
tions (typically 12 in. to 20 in. long) can be added to achieve a bed of any
reasonable length.
Although structural steel does not have the damping ability of cast
iron, it makes a good, solid bed if the weldments are designed properly.
Steel also makes longer beds possible at reasonable cost. You can even
make a "stretched" structural-steel bed by obtaining lengths of matching
steel from a steel fabricator.
I've seen two lathes with beds made from aluminum extrusions.
Extrusions don't have much to offer as a bed material for anything but
a miniature lathe, so I would avoid them on a full-sized lathe.
In a bed, you should look for rigidity and workmanship. The ways
should have a smooth surface, and the distance between them should be
constant. Make sure the tailstock and tool base slide easily but lock solid
where you put them. Test the truth of the bed by checking the alignment
of the headstock and tailstock (see the sidebar on p. 23).
THE HEADSTOCK
The business end of any lathe-the part that drives the work-is the
headstock assembly. The headstock is fixed permanently at the left end of
the bed and consists of either a casting, a welded steel body, or an extru
sion that holds a spindle set in bearings. A pulley on the spindle is con-
Indexing
pin
Outboard
spindle
nose (typically
with same
thread as nose
but left hand)
Key fits
bed of lathe.
Cast-iron housing
A Typical Headstock
Bearings (typically
double-row ball bearings)
Indexing spacing holes
(typically 12, 24, or 60)
Spindle nose is a coarse,
right-hand thread.
Morse taper
socket (typically
#1, #2, or #3
for wood lathes)

STANDARD SPINDLE SIZES AND MORSE TAPERS
Spindle thread size Manufacturer Morse taper
Headstock Tailstock
5fs in. plain Shopsmith None
(unthreaded)
% in. x 16 TPI* Sears, Coronet, None or #1
Record, Beaver
7/S in. x 14 TPI Rockwell Homecraft #1
1 in. x 8 TPI Delta and many others #2
(most common spindle size)
1 in. x 12 TPI** Myford #2
1Ys in. x 8 TPI Oliver #2
1Y4 in. x 8 TPI General, Nova, #2
Woodfast, Vicmarc
M33 x 3.5mm Oneway #2
(with locking groove)
1Y2 in. x 8 TPI Conover, Powermatic, #2 or #3
Atlas, South Bend
1Y2 in. x 6 TPI Union Graduate #2
(Harrison)
*TPI = threads per inch **Whitworth thread (54° flank angle, rather than 60°)
nected by a belt to a motor, which is normally mounted below or behind
the headstock (see the illustration on the facing page).
Spindle The spindle, a threaded shaft mounted horizontally, is the heart
of the headstock. It accepts the drive centers, faceplates, and other acces
sories that hold and power the work. Spindles are either hollow or solid
and range in size from l� in. to ll� in. dia.
The spindle size you need depends on the type of turning you intend
to do. For turning spindles between centers, you can get by with a small
diameter spindle. A common spindle size that is adequate for medium-duty
work is 1 in. For heavy-duty faceplate turning and architectural turning,
you will need at least a IlJ4-in. spindle that will not flex under load. Watch
out for spindles with odd thread sizes or odd taper sizes-what may seem
like a bargain will be no bargain at all if you can't easily obtain accessories
to fit the spindle. The chart above lists common spindle sizes for which
you have a good chance of readily finding accessories.
You should give much consideration to the spindle when choosing a
lathe. The most important thing to look for is a hollow spindle that is
machined to accept Morse-taper accessories. Morse tapers lock in place
when inserted into the matching tapered socket in the spindle.
More than any other feature, Morse tapers separate good lathes from
bad. Even if your turning needs are very casual, the advantages of Morse
#2
None or #1
#1
#2
#2
#2
#2
#3
#2
#2
Lathe Anatomy 13

Look for Morse Tapers
Morse tapers in both the headstock and the tailstock are water
shed features that separate serious
lathes from bad ones. Avoid purchas
ing a lathe without Morse tapers.
14 The Turning Machine
LATHE SIZE IS TYPICALLY specified in three ways, the first two of which are
closely related. The first measurement is center height-the distance
between the point of a drive center in the spindle and the top of the
bed-which determines the diameter of the work that the lathe can
accommodate. The second measurement is swing, which is double the
center height of the lathe. For standard spindle turning between cen
ters, a center height of 4 in. (yielding a swing of 8 in.) is adequate. For
heavy-duty bowl turning, a center height of at least 6 in. is desirable.
The third measurement of lathe size is the maximum distance obtain
able between the headstock and tailstock centers. This capacity deter
mines the maximum length of work that can be turned. For spindle turn
ing, 30 in. is the absolute minimum and 36 in. or more is preferable.
tapers are enormous. A Morse-taper socket in the spindle makes for quick
and easy mounting of drive centers and a host of other chucking acces
sories. Morse tapers lock when driven home and release with an equal
opposite force. They're universal, so you're not dependent on the manufac
turer for replacement accessories. By contrast, on a lathe that has a solid
spindle, all accessories have to be screwed on, which is not only time
consuming but also limits the range of accessories available and ties you to
the manufacturer.
Morse tapers are available in sizes #0 through #7 (see the chart below
for the sizes common to wood lathes). They have been widely copied in
the forms of other locking tapers, such as the American Standard taper,
the British Standard taper, the Brown and Sharps taper, and the lamo
taper. If you come across a used lathe with a taper size that does not appear
to be Morse, Machinery's Handbook (Industrial Press, 2000) will be a great
help. It lists dimensions for all types of locking tapers.
A further consideration is the height of the spindle above the bed,
which dictates the swing of the lathe and the diameter of the work that
can be turned (see the sidebar above). At its simplest, swing is double
the height of the spindle center over the bed. For example, a lathe with
a center height of 6 in. will swing 12 in. You have to be careful of manu
facturers' claims because they sometimes quote the swing over a "gap,"
which is a short dip in the bed just ahead of the headstock. This gap,
MORSE-TAPER SIZES
Size Dia. small end Dia. large end Length
#0 0.252 in. 0.356 in.
#1 0.369 in. 0.475 in.
#2 0.572 in. 0.700 in. 3Ya in.
#3 0.778 in. 0.938 in. 37/a in.

which is typically about 2 in. deep, allows you to turn larger-diameter face
plate work in this area. The problem is that when work extends into the
gap you can work only on the face (the exposed side) of it.
Unfortunately, twice the center height above the bed is not a true
measure of capacity. A better yardstick is to measure the distance from the
top of the tool base to the center of the spindle. Doubling this will give
you the true swing, which is the diameter of work the lathe will swing
between centers. A lot of faceplate turning also requires placing the tool
base under the work.
Bearings Bearings hold the spindle rigidly in place and allow it to turn
with a minimum of friction. They're an important consideration when
buying a lathe. The problem is that bearings are much harder to judge on
cursory examination than features such as the construction method or
spindle type.
Historically, lathes have run on plane cast-iron bearings, sleeve bear
ings, and babbitt bearings (see the illustration on p. 16), but most lathes
made today have rolling-element bearings. These include ball, roller, and
tapered-roller bearings (see the photo below right). Of these, ball bearings
are by far the most common type used in lathe construction. Each bearing
Tool-rest height dramatically affects
swing. This tool rest comes from a lathe
that advertises a 16-in. swing. The stan
dard tool rest for this Nova 3000 is much
higher than the tool rest for a Conover
lathe, which yields about 2 in. of extra
swing over the rest.
Today most woodturning lathes have at
least one set of double-row bearings.
Shown here is an SKF angular-contact
bearing of the type put in the best ma
chines. (Photo courtesy SKF bearings.)
True Swing
The true swing of a lathe is twice the center height over the tool rest,
not the bed as most manufacturers
state in their literature.
Lathe Anatomy 15

Bearing Quality
In reality there is little you can tell about the quality of the bearings of
any given lathe without taking the
machine apart. Fortunately, most
manufacturers use bearings that are
more than adequate for the duty
rating of a machine.
16 The Turning Machine
I
I
Plane Bearings
This simple cast-iron bearing is adjusted by
placing shims between the two halves and
tightening the two cap screws.
consists of an inner race and an outer race that are separated by a series of
steel balls. The opposing ends of the spindle ride on these rings of balls,
which provide a precise hold and allow the spindle to turn with a mini
mum of effort. The majority of the power from the motor can now be used
for productive work.
Bearings can sometimes be upgraded, which I will discuss on pp. 149-155.
Outboard turning feature Because some work will be too large in
diameter to swing over the bed, lathe manufacturers often design the head
stock so that work can be mounted on the outboard side. Outboard turn
ing is accomplished in two basic ways. One is to put a left-hand thread on
the outboard end of the headstock spindle and mount the work so that it
faces away from the lathe. The other option is to design the headstock so
that it pivots at right angles to the bed.
When work is mounted on the outboard end of the headstock, the
swing of the lathe becomes double the distance from the center of the
headstock spindle to the floor. Although this may sound like an ideal solu
tion for turning large-diameter work, outboard turning presents a number

of problems, the greatest of which is speed. Many lathes do not have a low
enough speed range to turn anything greater than 12 in. in diameter. For
large-diameter turning, you need a bottom speed of 150 rpm to 300 rpm.
Another problem with outboard turning is that there is no place to
support the tool rest. You have to use a floor-stand rest (typically a tripod
stand that holds the rest), but this device is not as solid as a standard rest.
In addition, this method of outboard turning sometimes requires a second
set of left-hand-threaded faceplates, and it demands that you do everything
in reverse of your normal way of turning. (Delta makes many of its face
plates threaded in both directions, which means they can be screwed on
either end of the spindle.)
Some lathes that use the outboard end of the spindle for outboard
turning have a special tool base attached rigidly to the lathe, which is a
much better setup. In effect, this creates a small bowl lathe that is a mirror
image of the actual lathe.
The second option for outboard turning, the swing-head design, is
well adapted to light-and medium-duty lathes. In a swing-head lathe, the
headstock pivots at right angles, and the work is turned in front of the
lathe (see the photo at left on p. 18). A special tool base attaches to the
base of the headstock into which the tool rest fits. Although such a setup
allows only a limited outboard swing of about 16 in. to 20 in., it's a better
arrangement for a number of reasons. First, the diameter of the work is
limited to within the low-speed range of the lathe. Second, the tool base
is attached rigidly to the lathe bed, making turning sure and safe. Third,
Oneway offers a short bed that can be mounted outboard (opposite the standard bed that
comes with the machine), which turns the machine into a bowl lathe. This offers great con
venience to a serious bowl turner because he has much better access.
A floor-stand rest allows outboard turning,
but you must have a lathe with low enough
speed to handle this kind of diameter.
Lathe Anatomy 17

Most manufacturers of today's light-and
medium-duty lathes handle outboard turn
ing by allowing the head to pivot. This
gives reasonable outboard capability with
out having to go to a floor-stand rest or
buy left-hand faceplates.
18 The Turning Machine
Indexing allows the locking of the headstock spindle at precise locations for purposes of
layout (such as a clock face), hand operations (carving flutes), or machine operations
(milling reeds with a router). Most manufacturers offer at least 12 positions, with 24 or
60 being the common numbers.
turning is in the same direction and orientation as takes place over the
bed. Finally, a second set of left-hand-threaded faceplates is not required.
It has been my experience both in selling lathes and advising buyers
of lathes that turners place unnecessary emphasis on turning outboard. In
reality, outboard turning is something that most people will do only once
or twice in their lifetimes, if at all. Don't have tunnel vision about the out
board feature, ignoring all the other useful features that a lathe should
have and that you will use every turning session. You can always rig some
thing up or borrow a lathe for the once-in-a-lifetime big job.
Index heads Some headstocks are fitted with an index head, which is a
mechanism that allows the spindle to be locked at equal intervals so that
layout or auxiliary operations can be performed. Examples of such applica
tions include laying out a clock face or a fluting pattern on a bowl or
milling reeds or flutes in a column with a router (see pp. 102-104). The
most common setup for indexing is a series of holes drilled in the head
stock drive pulley (see the photo above right), which is mounted on the
spindle. A pin in the headstock casting slides into the appropriate hole
and locks the spindle in place. Common hole patterns are 12, 24, and 60.
I like the 24-stop configuration because it allows me to divide the circum
ference of a workpiece into many different but equal sets of parts: 24 (for
fluted bowls and the like), 12 (for clock faces), 8 (common for period
furniture shapes), 6 (also for furniture), and 3 (I have never used this).
Indexing is a feature that mayor may not be of value to you. I have
spoken to many turners who have never used the index head. For certain

types of period-furniture turning, such as fluted legs, it is essential. If you
are considering a dandy lathe at a bargain price but it lacks indexing, buy
it anyway. An index head can be added later if you need it. There are sev
eral after-market chucks that incorporate the feature, or you can rig some
thing up yourself. Note that on most lathes the index head should not be
used as a spindle lock for removing faceplates because doing so may bend
the indexing stop. Most lathes have other provisions for locking the
spindle for faceplate removal.
MOTORS, BELTS, AND PULLEYS
Almost all woodworking lathes are supplied with a single-phase induction
motor. The motor typically mounts inside the stand or at the back of the
headstock and is connected to a pulley on the spindle by a belt. For small
lathes, l� hp is adequate, whereas bigger machines require 1 hp or even
11� hp. Mini lathes can get by with as little as lJ4 hp. Machines imported
from Asia frequently have power specifications on the motor nameplates
that are optimistic. Often such machines are quite serviceable otherwise,
so the best course is to replace the anemic motor with a U.S. model if it
lacks the desired power or burns out.
Increasingly, manufacturers are putting variable-speed direct-current
(DC) and alternating-current (AC) motors with solid-state controllers on
lathes. Today's solid-state circuitry allows the use of controllers that effi-
A DC motor is a nice way to add variable speed to an existing lathe. Many manufacturers
now offer DC (or variable-cycle-rate AC) as the method of variable speed.
Adding Variable Speed
The easiest way to add variable speed to an older machine is to
install a DC motor and controller or a
three-phase AC motor and a solid
state variable-cycle rate controller.
Lathe Anatomy 19

V-belt and pulley
V-belt wedges in pulley,
giving positive drive.
20 The Turning Machine
ciently make DC current from ordinary single-phase household current.
This makes it possible simply to dial a speed, which is much more conven
ient than having to move a belt by hand to change speed. Such a con
troller cannot be used with a standard induction motor; it requires a DC
motor. DC variable speed requires both a controller and a DC motor.
For variable-speed AC, a solid-state single-phase controller is attached
to a standard three-phase motor. The controller takes your 60-cycle single
phase electrical house (or shop) current and delivers three-phase current
at an any cycle rate between about 2 and 65 cycles. The speed of AC
induction motors is controlled by the cycle rate of the current, so slowing
the cycle rate slows the motor. With this system, the motor is inexpensive
but the controller is about the same price as a DC motor and controller
combined.
Either AC or DC solid-state controllers work beautifully and are my
preferred form of power. The drawback to both AC and DC variable-speed
power is cost. They are expensive-$500 and up. Still they offer the easi
est (and often the cheapest) way to add variable speed to a lathe that does
not have this feature.
Drive Pulley Systems
One-half of pulley
slides sideways on
shaft as speed
control is adjusted,
varying width of
pulley and changing
its diameter.
Variable-speed V-belt
Belt rides up and down as
diameter of pulley changes.
This side
is fixed.
Poly V-belt
Belt combines positive drive
of standard V-belt with
constant speed of flat belt.

The original drive system for connecting lathes to a power source was
a flat leather belt. A three-or four-step set of matched pulleys gave a good
range of speeds for the turner. Although flat leather belts gave very con
stant speed with no surging, they tended to slip, thus wasting power.
Most lathes made in recent years use V-belts for power transmission.
V-belts drive positively because greater tension on the belt causes it to
wedge tighter in the pulley groove. An additional advantage of V-belts is
that manufacturers can provide variable speed by installing a variable
width pulley set (see the illustration on the facing page). A mechanical
control adjusts the width of the drive pulley, which effectively changes the
pulley diameter and thus the speed. Moving the two halves of the drive
pulley apart decreases the diameter (and decreases the speed); squeezing
the halves back together does the reverse.
The mating pulley on the headstock is similarly split but is spring
loaded so it automatically adjusts to the state of the drive pulley. This
setup gives a wide range of infinitely variable speeds. The only drawback
to such a speed-control system is that it wears out belts faster, necessitating
annual belt replacement for a lathe that gets moderate to heavy use.
A recent innovation is the poly V-belt, which is a flat rubber belt with
a series of small V-ribs machined on the inside surface (see the illustration
on the facing page). This design gives the belt the positive drive character
istics of a V-belt with the constant velocity of a flat leather belt. Many
newer lathes run on poly V-belts.
THE TAILSTOCK
The tailstock assembly is composed of the main casting, a spindle (or
ram), a spindle-locking lever, a hand wheel, and a mechanism to secure the
unit to the lathe bed. Whereas the headstock is stationary, the tailstock
can slide along the bed to accommodate work of varying lengths and can
be locked at the desired distance from the headstock.
The advantages of a good tailstock should not be overlooked because
it does much more than just hold a center. As with the headstock spindle,
the tailstock spindle should be machined to accept Morse-taper acces
sories. Look for a spindle equipped with a #1, #Z, or #3 Morse taper. The
tailstock spindle sometimes runs a bit smaller than the headstock spindle.
For example, if the headstock spindle is 1 liz in. dia., the tailstock spindle is
typically 1 in.
An important aspect of tailstock design is spindle travel-the amount
the spindle can be moved when the tailstock is locked to the bed. Lathes
typically have about Zllz in. of spindle travel, which is adequate for most
applications. I prefer to work with a tailstock spindle that can move as
much as possible because the tailstock itself doesn't have to be moved as
often.
The tailstock spindle is advanced and withdrawn by turning a hand
wheel, which is no more than a large nut. A lever on top of the tailstock
locks the spindle in place and prevents it from drifting due to the vibra-
A common tailstock design uses a left
hand thread on the outside of the spindle.
The left-hand thread is necessary to make
the adjustment logical-turning the hand
wheel right advances the spindle and vice
versa. This also allows a hollow spindle for
drilling through the tailstock.
Lathe Anatomy 21

Checking a Self-Ejecting Tailstock
If you own a lathe with a self-ejecting tailstock, occasionally a taper will be
too short to eject. It is always good to
check any new accessory by lightly
inserting it and running the spindle
rearward to see if it ejects.
22 The Turning Machine
tion caused by turning. The traditional tailstock setup calls for the outside
of the spindle to be left-hand threaded (see the photo on p. 21). Because
the thread is left-handed, the spindle advances when the handwheel is
turned clockwise, which is normal to our way of thinking. This design is
typically used on cheaper lathes, although it is sometimes also found on
very expensive ones. Accessories are ejected by inserting a knockout bar
through the spindle.
A more elegant arrangement is a self-ejecting spindle. The inside of
the spindle is left-hand threaded, and a long left-hand screw extends from
the hand wheel into it (see the photo below). Turning the wheel to the
right advances the spindle, while turning it left withdraws it. As the spin
dle is retracted all the way rearward, the screw bumps the Morse taper in
the spindle and ejects it. A crank handle is often added to the handwheel
so that the spindle can be moved quickly.
The tailstock must lock securely to the bed and not move while you're
turning. There is a variety of locking mechanisms, ranging from a stud
running down between the bed rails with a plate and a nut to complicated
cams. The main thing to look for is a good positive lock that will hold the
tailstock without its drifting backward when you apply pressure to the
work with the hand wheel.
A more elegant design is the self-ejecting tailstock, which automatically ejects the Morse
taper in the spindle when the spindle is fully withdrawn. You cannot drill through such
spindles, however.

WHEN YOU BUY A NEW LATHE, it's a
good idea to check that the tail
stock aligns with the headstock.
(This test will also check the truth of
the bed.) The best gauge for test
ing center alignment is a pair of 60°
dead centers (see pp. 43-45), but
any set of Morse-taper accessories
that come to a point at the center
will work. Simply put one center in
the tailstock and one center in the
headstock, then slide the tailstock
forward until the two points touch.
The centers should align perfectly.
Center alignment is important in
faceplate work but relatively unim
portant for spindle turning. Although reasonable center alignment is advantageous (if for no other reason
than that the tool rest aligns with the work), center alignment could vary by 'fa in. or more on a 15-in. spindle.
The longer the turning, the more out of alignment the two centers could be. Center alignment is especially
important if you plan to do any metal spinning with your lathe. Woodcraft Supply Corp. sells a clever double
ended #2 Morse taper for checking spindle alignment, as shown above.
THE TOOL BASE AND TOOL REST
What we tend to think of as the tool rest is actually composed of two
parts-the tool-base assembly and the tool rest itself. The tool base, which
supports the tool rest, attaches to the bed of the lathe and can slide to any
point between the headstock and the tailstock. The base (known as the
banjo in England) also moves in and out so that the tool rest can be posi
tioned right next to the workpiece. Desirable features in a tool base
include ease of movement, rigidity, and a low profile. The latter feature
is important because the height of the base affects the swing of the lathe.
For each Ys in. that the tool-base height is reduced, you are rewarded with
an extra Y4 in. of swing.
The tool base must lock down securely and not slide under load. The
hold-down/locking mechanisms range from wedges under the bed that are
pounded snug with a mallet on classic wood-bed machines to a simple nut
and bolt that are tightened with a wrench on economy lathes to compli
cated lever-operated cam mechanisms on full-featured machines. With
each level of sophistication come commensurate increases in price. When
choosing a lathe, the best course is to try the tool base to see how it oper
ates. Move it to a variety of angles and positions, lock it in place, grab it
with both hands, and see if you can move it. Don't be afraid to throw some
body weight into this exercise.
Lathe Anatomy 23

24 The Turning Machine
A full-length wood rest works just fine for turning long stair balusters.
The tool rest provides a fulcrum point for support and control of tools
during turning. The rest mounts in the tool base and is adjustable to any
height and angle. A locking mechanism (ranging from a simple knob and
stud to a cam) secures the rest in the tool base. The front surface of the
rest should have sufficient slope so that any tool will contact only the top
edge in any turning operation.
The tool rest should be of solid construction. Cast iron is the tradi
tional material, but structural steel performs just as well and wood may also
be used. Lathe manufacturers offer tool rests in standard lengths of 6 in.,
12 in., 18 in., and 36 in., but sometimes the longer rests require two tool
bases. For special turning situations, you can have a local welder fabricate
a longer rest from structural steel, or you can make your own full-length
tool rest out of wood (see the illustration on the facing page).
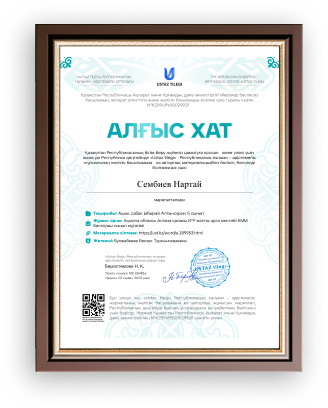
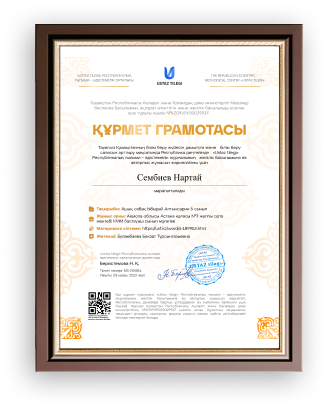