Эксплуатация
станков
Эксплуатация
станков представляет собой систему мероприятий,
включающую транспортирование и монтаж станков, их настройку и
наладку, контроль геометрической и технологической точности, уходи
и обслуживание.
Транспортирование станков необходимо
осуществлять строго по инструкции, указанной в руководстве по
эксплуатации. Перемещать станки по цеху можно лишь волоком на листе
или а специальной тележке. Тяжелые станки для удобства ремонта
располагают в зоне действия подъемно-транспортных
средств.
Станки нормальной точности, легкие и средние,
устанавливают на общее бетонное полотно цеха с тщательной выверкой
положения уровнем и регулировкой с помощью клиньев. Надежное
крепление осуществляется посредством фундаментных болтов и заливкой
основания станка бетоном.
Точные и
тяжелые станки устанавливают на индивидуальные фундаменты. Также на
индивидуальные виброизолирующие фундаменты устанавливают станки с
большими динамическими нагрузками и повышенной вибрацией при
работе, для того, чтобы изолировать станок от другого оборудования
и воспрепятствовать передачи колебаний через грунт. С той же целью
станки устанавливают на виброизолирующие
опоры.
Если
станки транспортируют в частично разобранном состоянии, то после
установки их монтируют. Выполняют заземление, подводят
электропитание и, если это необходимо, соединяют коммуникации
центральной подачи смазывающе-охлаждающей жидкости,
стружкоудаления, сети сжатого
воздуха.
Наладку и настройку станков производят также
в строгом соответствии с руководством по
эксплуатации. Наладка - это
совокупность операций по подготовке и регулированию станка,
включающих настройку кинематических цепей, установку и
регулирование приспособлений, инструментов, а также другие работы,
необходимые для обработки деталей.
Настройка - это
регулирование параметров машины в связи с изменением режима работы
в период эксплуатации. Со временем настройка станка частично
нарушается, и периодически требуется её восстановление
(подналадка).
На
универсальных станках настройку режимов резания производит
станочник непосредственно перед или во время обработки,
устанавливая рукоятками частоты вращения шпинделя, подачу и глубину
резания. На специальных и специализированных станках режимы резания
устанавливаются заранее, согласно карте наладки, путем установки
сменных колес в цепях главного движения и подач. Наладку завершают
регулировкой инструментов на размер и пробными
работами.
Геометрическую
точность станков
проверяют в соответствии с ГОСТами. Суть проверки заключается в
контроле точности и взаимного расположения базовых поверхностей,
формы траектории движения исполнительных органов (например, биение
шпинделя), в проверке соответствия фактических перемещений
исполнительного органа номиналу (например, точность
позиционирования, кинематическая
точность).
Технологическую
точность, которая
относится в большей степени к специальным и специализированных
станкам и станочным системам, контролируют перед началом
эксплуатации оборудования. Для этого на станке обрабатывают партию
деталей, измеряют их и с использованием методов математической
статистики оценивают рассеяние размеров, вероятность выпадения
размеров за пределы заданного допуска и другие показатели
технологической точности.
Уход и
обслуживание включает
чистку и смазывание, осмотр и контроль состояния механизмов и
деталей, уход за гидросистемой, системами смазывания и подачи СОЖ,
регулировку и устранение мелких неисправностей. При эксплуатации
автоматизированных станков применяют смешанную форму обслуживания:
наладку производит наладчик, а подналадку - оператор. При этом
функции оператора разнообразны: приемка заготовок и их установка,
снятие готовых деталей, оперативное управление, периодический
контроль деталей, смена или регулирование режущего инструмента,
регулирование подачи СОЖ, контроль удаления стружки и
др.
Уход за
гидросистемой предусматривает контроль температуры
масла, которая обычно не должна превышать 50 градусов по Цельсию.
Первую замену масла в гидросистеме, как правило, производят через
0,5-1 месяц работы, чтобы удалить продукты притирки механизмов. В
дальнейшем замену масла производят через четыре-шесть месяцев.
Необходимо систематически контролировать и поддерживать уровень
масла, следить за состоянием трубопроводов, чтобы не было утечки и
не попал воздух в гидросистему, регулярно проводить чистку
фильтров.
Уход за
электрооборудованием включает
ежемесячную очистку аппаратов от пыли и грязи, подтягивание
винтовых соединений, контроль плавности перемещений и надежность
возврата подвижных частей электроаппаратов в исходное положение.
Периодически смазывают приводы аппаратов тонким слоем смазочного
материала, не допуская попадания его на контакты. Раз в полгода
меняют полярность рабочих контактов у кнопок и выключателей,
работающих в цепях постоянного тока, проверяют состояние контактов.
При появлении пригара или капель металла на поверхности контактов
их слегка зачищают бархатным надфилем (зачистка абразивными
материалами недопустима!!!).
Особенности эксплуатации
станов обязательно указывают в инструкции по
эксплуатации. Соблюдение инструкций обеспечит длительную,
бесперебойную работу оборудования.
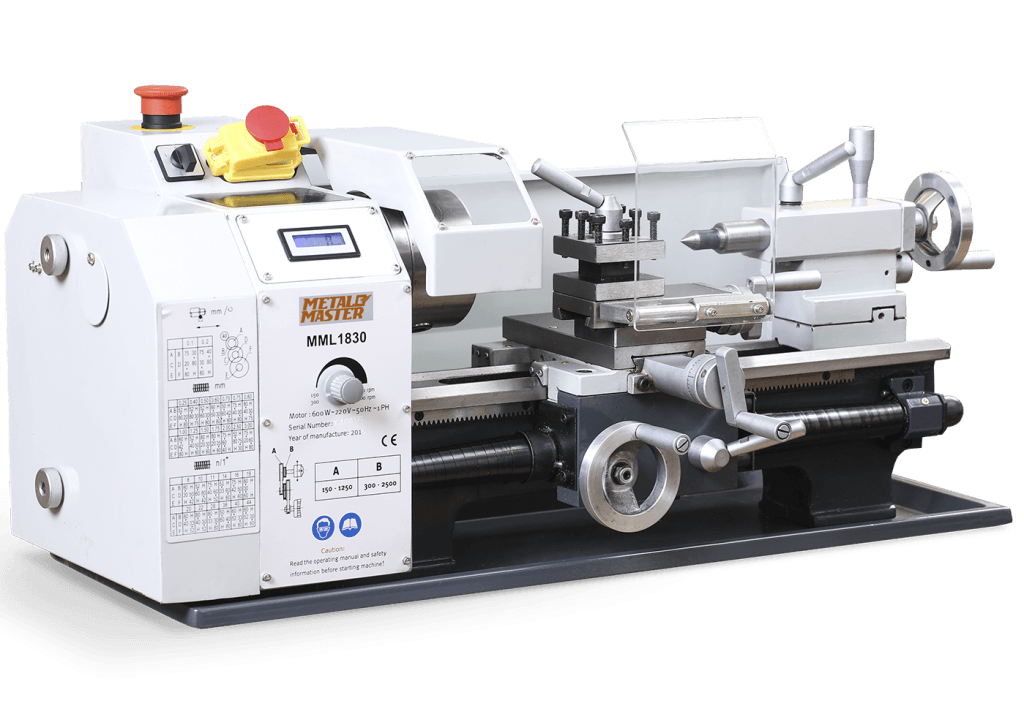